Jan 21 | 2021
Breathtaking Scale of Fehmarnbelt Project
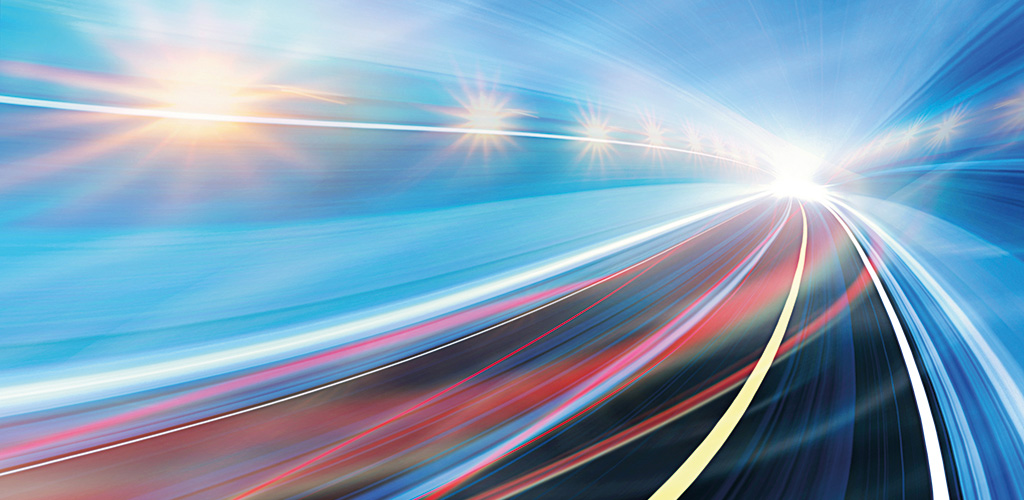
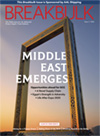
More than 18 kilometers long and incorporating a four-lane motorway and twin-track electrified railway, the Fehmarnbelt Tunnel will be a record breaker as the world’s longest combined road and rail immersed tube tunnel.
Its construction will be something of a repeat performance for Denmark, as the Øresund Tunnel, part of the fixed link between Denmark and Sweden, was built as a similar immersed solution 20 years ago. The difference? The Fehmarnbelt Tunnel, across the Baltic Sea, will be more than five times the length.
The scale of the project is breathtaking. The planning is immense. Lars Greiner, bulk terminals specialist at Hamburg Port Consulting, put it into context: “I have worked on projects like this before, where on the face of it looks very big – but it is just like ‘how do you eat an elephant?’ The answer is you break it down into phases.”
In this case, it all starts with a port – a brand new one, being built at Rodbyhavn on the island of Lolland. This will be a largescale work harbor, providing 1,500 meters of dedicated quays with water depth of 10.3 meters.
Alongside, an immense construction operation is being built from scratch, to include production halls and drydocks.
Eight production lines will create concrete tunnel segments in a continuous casting process. Nine segments will be joined together to create each complete tunnel element, 217 meters long, 42.2 meters wide and 8.9 meters high, and weighing 73,500 tonnes. The finished elements, fitted with watertight bulkheads, will be moved into the drydock, floated out into the harbor and then towed to a holding area out at sea, ready to be immersed in a pre-excavated trench. The tunnel will consist of 89 elements.
Three major contracts
The Fehmarnbelt Link, connecting the Danish island of Lolland and the German island of Fehmarn, is a completely Danish project, albeit involving some obligations from Germany regarding provision of road and rail links on the German side. Femern A/S is the Danish state-owned company charged with delivering the tunnel, which will be paid for by customer tolls when it opens for traffic.
The project is divided into three big contracts – “tunnel north,” “tunnel south” and portal/ramps on both sides. All three contracts have been awarded to the one joint venture, Femern Link Contractors, or FLC.
“We started with only the land at Rødbyhavn; we will build the big factory to produce the tunnel elements and the harbor to bring in all the materials for production and to sail out the elements to the site,” said Tomas Skjold, construction manager, Femern A/S.
“We will have separate quays for different materials – i.e. one for reinforcement and gravel, and another for bringing in cement and all the materials for concrete. The supply of materials will be needed for continuous production of the tunnel elements.”
The big gain from this approach is the ability to have continuous progress, he said. “Normally when you are doing a tunnel, you are digging a big hole in the ground, bringing out the spoil, and then stopping while you take out two or three elements which are installed under the seabed, then restarting again.
“Also, we are building a tunnel for two lanes of traffic and two railway lines, so conventional tunneling would require a huge diameter. For a tunnel under the seabed, you would have to encroach more into the German and Danish territory at each end in order to get the tunnel low enough while also having the gradual gradient required for rail.”
The process will require a massive and continuous supply of raw materials, but no heavy-lifting at this stage.
Skjold said the logistics for larger items required later in the project – for example, electrical components, barriers, lighting, rails and so on – have yet to be decided. “At present the focus is on the civil contractors, and phases for the railway and mechanical/electrical installation will go out to tender at a later stage.”
The production of 3 million cubic meters of concrete will require 7 million tonnes of material to be brought into the harbor. As well as excavating a trench in the seabed, the design involves building a gravel bed and also using gravel and other materials on the side and top of the tunnel elements: “This will also require a huge amount of materials, about 14 million tonnes mainly of gravel and sand.”
By December 2020, work on the Rødbyhavn quays was 80 percent complete and dredging had begun. While FLC’s responsibility covers building the factory, producing the elements, then towing them out and lowering them into the trench, another contract covering dredging and reclamation was awarded to a Dutch consortium, Fehmarn Belt Contractors or FBC, and came into force in November 2019.
“Between 2,000 and 3,000 people will work on construction of the tunnel elements,” Skjold said. “Once you add in the local area, the supply chain and service suppliers, including accommodation, hospitality and smaller jobs around the project, a lot of people will be involved at its peak. Right now, about 150 people are working on construction of the harbor.”
The consortium is also building a small harbor on the German side next to Puttgarden.
Opportunities Beyond the Link
Greiner said now that work on the tunnel work has started, the sector can “look forward to new opportunities” across the project logistics sector. “This connection between Denmark and Germany is already laying the foundations for investment and expansion across many industries, with the promise of associated project cargo requirements.”
He pointed out that the Fehmarnbelt link is one of the five cross-border projects within the European Union’s Trans-European Transport Network (TEN-T) policy, whose ultimate objective is to close gaps, remove bottlenecks and technical barriers, and strengthen social, economic and territorial cohesion in the EU.
“The hope is that this development will move much of the logistics movement from the Great Belt route via Zealand in Denmark to a more direct route between Copenhagen and German, smoothing trade between them.”
Theis Gisselbaek, chief commercial officer at the Danish port of Grenaa, has also spoken of the possibility of gaining work linked to the Fehmarnbelt project – and he also thinks the knock-on opportunities could be considerable.
“Infrastructure-wise, a lot of projects will be materializing in the next five to seven years, as the [Danish] government tries to create work around Covid-19. We are a project port, so it could be good for us,” he said. “We are focusing on the tunnel construction itself but also on a lot of other projects which we expect to see close to the tunnel – general infrastructure, building work and so on.”
Grenaa could handle steel and other building materials required for the construction of the factory, as well as providing a hub role for bulk materials during the tunnel construction, he said.
“We have heard that some materials will be coming from China – steel for armored concrete, for example – and this would likely involve 30,000-40,000 tonnes in one vessel. The project is based around just-in-time delivery for everything, so this might require a hub function with reloading into small vessels to deliver to the site. We might also see shipments of steel rails for the railway later on.
“A lot of vessels and machinery will be required for the project, and these will need a maintenance and stacking facility if they have an ideal period. We believe the Port of Grenaa is well placed to provide facilities for vessels and storage for cargo.”
The knock-on benefits from the new tunnel link are also significant for the region of Lolland-Falster, he said. Motorists will be able to make the crossing in 10 minutes and train passengers in seven minutes, instead of an hour-long ferry ride or a 160-kilometer detour through the region of Jutland in Denmark.
The area had a major industrial production cluster in the 1950s, ’60s and ’70s, but many factories closed down in the 1980s. “The area has suffered since then, being in the middle of an area with no logistics or transport routes. We are already seeing a build-up of logistics hubs around the highway between Copenhagen and the island of Falster and the railway is being updated, so the effects have already begun.”
Future Port Question
While Rødbyhavn will play a crucial role as possibly the world’s largest work harbor, its future is not certain. At present, Femern’s permit states that the factory will be demolished, and the harbor returned to its previous state once the project is finished. Any alternative decision would be a political one, Skjold said.
However, Gisselbaek added that the Rødbyhavn facility may eventually be maintained to meet the needs of other infrastructure developments. Among these is the much-discussed possibility of building a Kattegat crossing in the form of a tunnel, a bridge or both.
“Apart from that, with the huge progress in offshore wind expansion off Denmark and other major projects, we believe that the capacity of port infrastructure around Denmark and the region will be limited and we expect to be extremely busy,” Gisselbaek said.
Felicity Landon is an award-winning freelance journalist specializing in the ports, shipping, transport and logistics sectors.
Image credit: Shutterstock