Apr 13 | 2020
The Importance of Planning Well Before Material Moves Multimodally
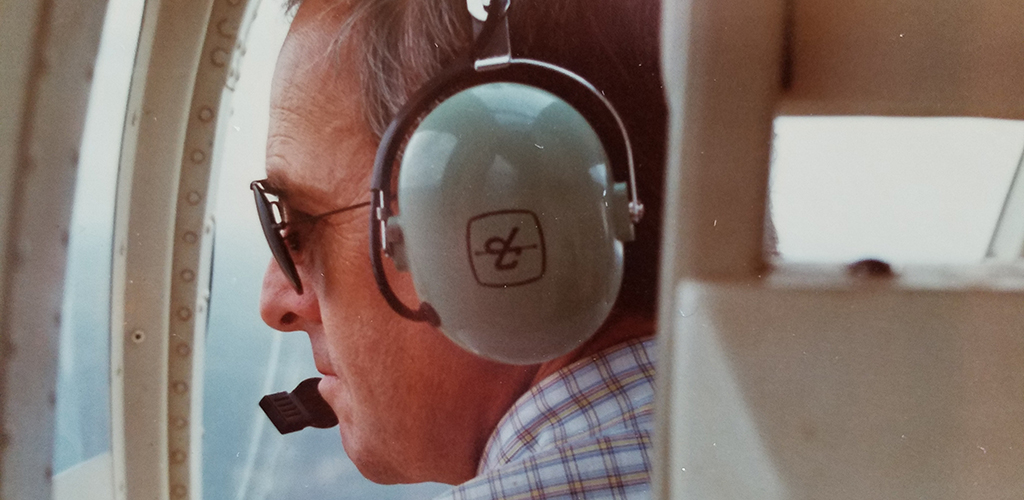
By John Amos, Breakbulk Americas Advisory Board, Member Emeritus
This article is part of a new series featuring stories about complex logistics projects from Breakbulk veterans. In today’s cost cutting climate, these first-person accounts from some of the best minds in the business present lessons from the past that can be applied today. —Leslie Meredith, Marketing & Media Director
In the late 1980s, two major engineering, procurement and construction companies had a joint venture to develop a huge iron ore project in the highlands of Papua New Guinea. It was called the OK Tedi Project and had complex logistics requirements and schedules in one of the most remote areas in the world and extreme weather conditions. The project scope was to build facilities to mine a mountain of iron ore topped with 1 million ounces of gold. The joint venture team was committed to teach the local inhabitants skills far beyond their agrarian lifestyle and use wheeled equipment.
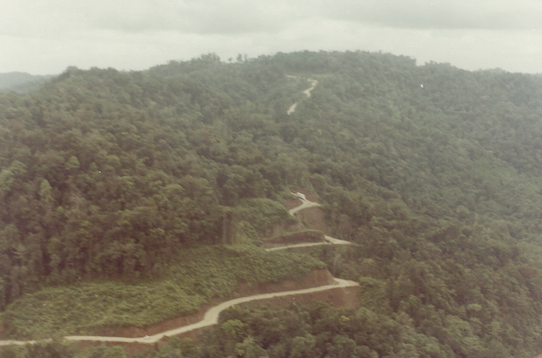
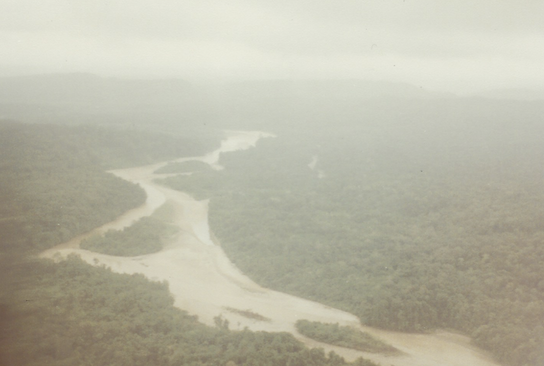
Priority cargo was scheduled for the flights, and one of the highest was gasoline in large rubber bladders.
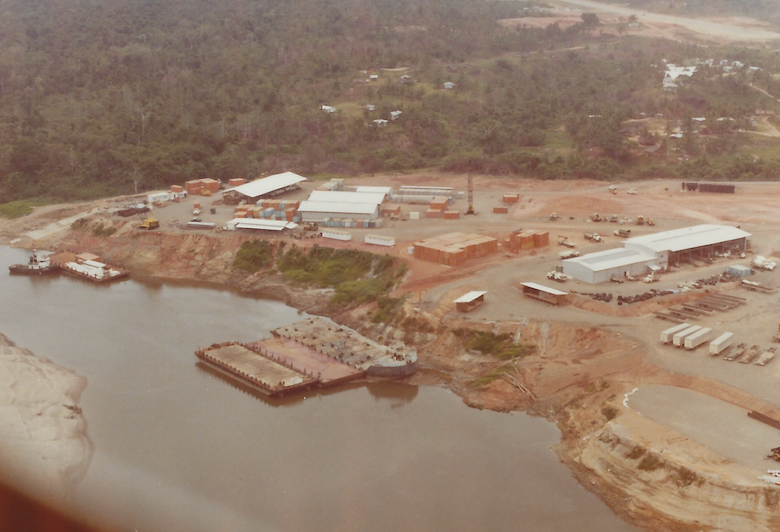
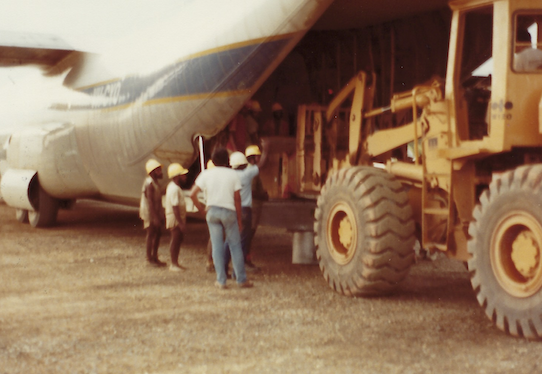
This unusual project is a good illustration of how important it is to plan the movement of project material well in advance of the first movement of project cargo. This is extremely important when multiple modes of transportation are utilized, including ocean, barging and a haul road, and encountering frequent poor weather.
More from Amos
- Iraq: Long-term Planning Vital for Critical Operations Involving Employees, Families Under Dangerous Conditions
- Extreme Logistics: Kuwait Oilfield Fires
John Amos is an international logistics and transportation consultant specializing in issues related to planning, operations and regulatory issues. His experience encompasses the fields of ocean, air and surface transportation. For more than 45 years he has had international and North American positions in the fields of logistics, procurement and construction management.
You can reach John Amos by email at [email protected].