Sep 04 | 2020
An extraordinary account of COVID-19 challenges around massive crane delivery at Port of Riga
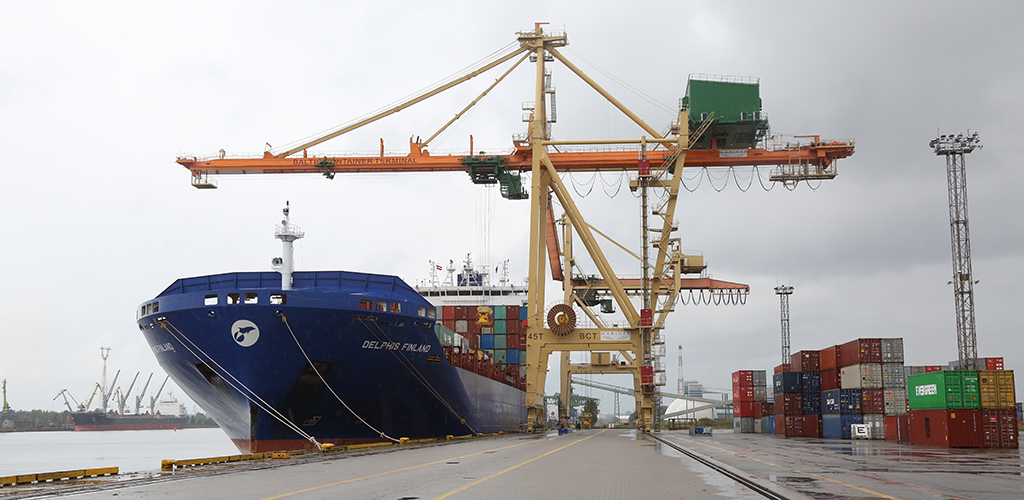
On 25 August, Sany Europe celebrated the delivery of its large Ship-to-Shore Container Crane STS454701 to the Port of Riga for Baltic Container Terminal Ltd. But the convivial atmosphere belied the difficult transport complicated by the COVID-19 outbreak.
“The successful delivery, however, was not a plain sailing,” a Sany representative said in a statement. “On the contrary, it was fraught with challenges.
“On 12 May 2020, the equipment arrived in Riga on schedule in the form of a complete machine. Yet that was just the time that COVID-19 dashed around the world. Although the goods had arrived, the people’s arrival has been severely affected by the epidemic. The entire European Union had been closed since March, and Latvia, as a member state, had also had over 1,000 confirmed cases.
However, in order to protect the logistics timetable, BCT sent a call to Sany after the arrival of the goods, which indicated that it was urgent to install the crane immediately, so as to put it into use as soon as possible. The customer’s call is the order, thus Sany quickly organized a team of five senior engineers and began to make all kinds of preparations for departure.
The biggest difficulties were visa and entry issues. Under the European Union’s epidemic control policy at the time, the team of engineers could not enter Latvia. Sany contacted the Latvian Embassy in China to explain the situation, while BCT reached out to the Latvian Ministry of Commerce, Ministry of Interior and other national departments to apply for approval.
As the urgency and importance of the situation was conveyed clearly, the Latvian government was also impressed by the professionalism of the Chinese company. The Latvian government praised Sany for its great sense of responsibility, especially during the epidemic, for the fact that a group of Chinese people were willing even to risk their own health to benefit a friend country. Subsequently, the Latvian Government granted special entry permits and the Embassy granted Schengen visas, making it possible for the engineers to deploy.
After the visa, the Sany team then faced another difficulty: there was no direct flight from China to Latvia, so they had to transfer to Germany first. But because of thepandemic controls, the engineers were not allowed to pass through the German customs and to enter the transit zone. This meant they could not take any of the Frankfurt-Riga flights. The only solution was to fly to Frankfurt by private jet rather than enter the transit zone.
Although the cost of the private jet charter was high, Mr. Deng Haijun, Director Port Machinery for Sany Europe approved the expense. “Chartering a flight is expensive,” he said. “But no way is it as expensive as [breaking] our promise to the customer.”
Five engineers in full body protective suits, goggles and masks arrived in Frankfurt on May 16 after a long trip with only 20 minutes to make the private flight connection: five minutes to collect luggage, eight minutes to change terminals and four minutes to go through security-check again. As if in a scene from “Fast & Furious,” when the five sprinted to the cabin door, they were only seconds from take-off.
But the challenges were just beginning. After a long sea journey, they faced the herculean task to restore, adjust and debug nearly one thousand tons of heavy and large equipment.
The first task was to unload the ship. During this period, the men worked super-long hours each day, fell into bed late at night, got up before dawn and finally finished unloading the ship four days later. For such a large equipment, it only took five men and four days to complete the unloading safely.
And in the subsequent recovery, rectification, and debugging tasks, the Sany engineers worked more very long hours on most days and voluntarily gave up all weekend breaks. They prepared simple fried rice on the dock every noon, but continued to pay close attention to every minute request from the customer—even the cleaning of a corner dozens of meters high.
At 8 a.m. on July 12, the equipment faced its 24-hour durability test. After more than ten hours of intense daytime concentration, the five men still needed to be fully ready for the night ahead. In the moonlight, one could still hear the trolley moving regularly on the track, the spreader lifting rhythmically, and the siren of the gantry moving from time to time. In order to overcome fatigue, the five shifted every two hours and took turns to rest, which meant just a short rest fully clothed on the hard machine room floor. At 8 a.m. on July 13, the test was finally over, and the computer printout showed that the test was passed.
On the morning of July 20, while the Sany team and BCT managers were waiting on the dock, the government acceptance officer arrived. He came to make a final check of the equipment. If all factors meet the safety standards required by the Latvian Government, the BCT would be granted a license for the use of the equipment, which is also the final element of the acceptance of the equipment. The team accompanied the officer up to the main room dozens of meters high, answering his questions and showing relevant technical data. As the officer walked down from the machine, he smiled and said to the crowd, “It’s a wonderful machine! You’ll get a permit soon.” And indeed, on the morning of 21 July, Mr. Gerard Sammut solemnly signed his name on the Acceptance Certificate.
