Oct 08 | 2020
Misidentified cargo, project manager quits, seized passport – lessons learned in the field
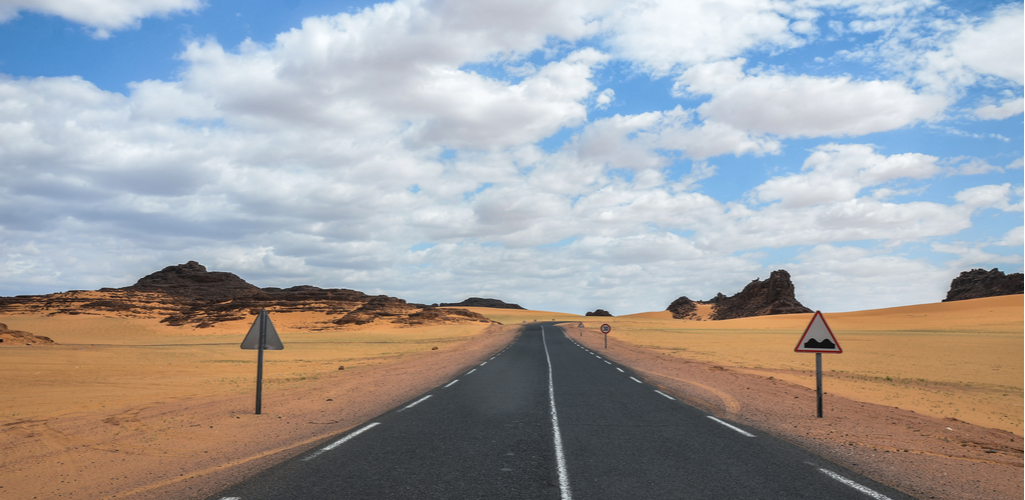
Breakbulk veteran John Amos recounts a particularly thorny job in Algeria, including misidentified cargo, a project manager who became frustrated enough to quit and a seized passport.
This article is part of a series featuring stories about complex logistics projects from Breakbulk veterans. In today’s cost cutting climate, these first-person accounts from some of the best minds in the business present lessons from the past that can be applied today. For more great stories visit the Breakbulk Veterans Hub —Leslie Meredith, Marketing & Media Director
During the construction of a large project in Algeria, a severe problem developed involving the large number of pumps and valves being delivered to the project on bi-monthly charter vessels. Financed by Export-Import Bank of the U.S. (EXIM), the project’s construction schedule was being affected because the high pressure pumps and valves had incorrect or non-existent manufacturer plates and the project could not rely on bill of lading descriptions.
This was compounded by the arriving crates being confused with those arriving for a Japanese project which was using markings similar to those for our project including using the same color coding on the crates for ease in identifying project crates at the congested port. I flew to the jobsite to review the situation and provide solutions.
Delivery from the port to the project was further compounded by port customs lack of cooperation and slow processing of documents. This could affect charter party laydays. Jobsite management placed the crates of pumps and valves in the laydown area at the project until the confusion could be resolved.
To make things worse, the project logistics manager told me that he was leaving the project due to the continuing problems he said “made it impossible to do a proper job.” He struggled with the client’s personnel who refused to speak English, being limited to one phone/fax line for outside communications and the incessant problems at the port.
While preparing an analysis and report so I could quickly advise the project office in the U.S. on steps to take to solve the problems, the logistics manager and I were stopped at an army roadblock on the highway from the port to the project. My passport was taken from me and placed in a file cabinet on the side of the road. In turn I was given a visitor’s badge with no details on it. I had to wait three days for my passport to be returned to me at the project office with no explanation. By this time, I was more than ready to leave the country.
For a different perspective on this Algerian project, read Brent Phelps’ “Pizza, Burgers and Christmas Trees as Project Cargo?”
The problems were not difficult to explain to the jobsite manager who I had met a year before while in Kuwait at the end of the first Gulf War. I stressed that the problems with the delivery of the pumps and valves, and all material, could be remedied by taking some very basic steps in better management of procurement procedures established for all company projects.
These included:
- Jobsite advising procurement support offices immediately whenever there is a problem with any material
- Closer management of the freight forwarder on how they marshaled cargo for the charter vessels
- Improve preparation of the enormous amount of documents required to eliminate mistakes including what was required by EXIM. (This was before the advent of extensive electronic documentation and advanced communications.)
- Improve final inspection of key construction material
Lessons Learned
The key lessons learned from this series of problems is that projects in remote areas with a long supply chain must start with a detailed logistics study that identifies those areas likely to cause problems. The study must be shared with project management, engineering, procurement disciplines and the client. With EXIM participation there must be a clear understanding of the bank’s requirements when it comes to the employment of ocean carriers and airlines.
About the Author
John Amos is an international logistics and transportation consultant specializing in issues related to planning, operations and regulatory issues. His experience encompasses the fields of ocean, air and surface transportation. For more than 45 years he has had international and North American positions in the fields of logistics, procurement and construction management.
You can reach John Amos by email at [email protected].
Subscribe to BreakbulkONE and receive more industry stories and updates around impact of COVID-19.