Apr 15 | 2021
Breakbulk Veteran John Amos recounts a multimillion-dollar transport up the Mississippi RIver
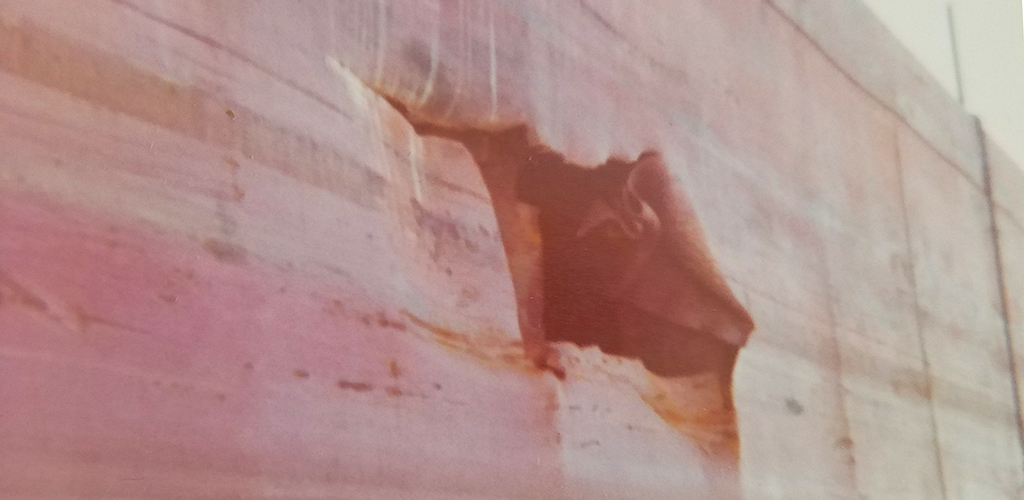
Logistics played a major role in shipping an 810-ton reactor pressure vessel (RPV) and 128-ton head from a fabricating facility in Memphis, Tennessee, on the Mississippi River to a jobsite in New Jersey via the Gulf of Mexico and Intracoastal Waterway. The RPV and head were loaded on a 200’ x 50’ cellular barge. Because the project was behind schedule, elements of planning and delivery were critical with heavy pressure coming from the client and project management. The shipping plan included keeping everyone advised of progress on a daily basis.
The First Delay
The RPV and head were loaded onto the barge at the face of the fabricator’s dock using a 1000-ton stiff- leg crane called “Ichabod.” At the last moment the first delay occurred. The water depth at the face of the dock was too low to safely lower the RPV onto the barge. The U.S. Corps of Engineers advised that it was raining in Pittsburg and that the water depth would increase by two feet in two days and that was what happened so the pieces were safely loaded and secured on the barge.
The Second Delay
The voyage down the Mississippi River and across the Gulf of Mexico was uneventful and movement slowly progressed up the Intracoastal Waterway. Pleasure craft are heavy users of the waterway so the tug captain took extra precautions. Then the second delay occurred while transiting South Carolina. A thick fog developed resulting in the tug captain putting into a port as a safety precaution. The two-day delay resulted in an extra cost which had to be absorbed by the construction company.
While the remainder of the voyage proceeded without incident preparations were being made for the discharge of the RPV and head near the jobsite. There was no dock anywhere near the jobsite so the discharge had to be onto the shore and to the jobsite on a prepared temporary road. Divers were hired to sweep the bottom of the shallow bay near the shore to ensure there were no obstructions that could damage the barge or tug and cause further costly delays.
Damage Discovered
As the barge neared shore the crew and discharge party on the shore noticed that the barge had been holed at some point during transit. The hole measured 6 by 8 feet mid-barge at the water line. The crew had no knowledge of when or how this occurred. The discharge was delayed while marine surveyors, insurance representatives, client representatives and construction company engineers made their assessments. As the barge was constructed entirely of individual cells the water in the barge was contained in the single damaged cell so the barge was stable and structurally sound and discharge proceeded without any problems. This event caused a one-week delay which added considerable cost that also had to be absorbed by the construction company, as was the cost to repair the barge.
Lessons Learned
The lessons learned started with ensuring project and construction management and the client clearly understood all elements of the barge/tug company contract, including damage and delay clauses that specify which party is responsible for payment in cases of delay and/or damage. Second, was the importance that all involved received daily updates on the progress of the movement. Multimillion dollar events such as this receive tremendous attention and everyone involved becomes a transportation “expert” with constant questions that must be answered.
About the Author
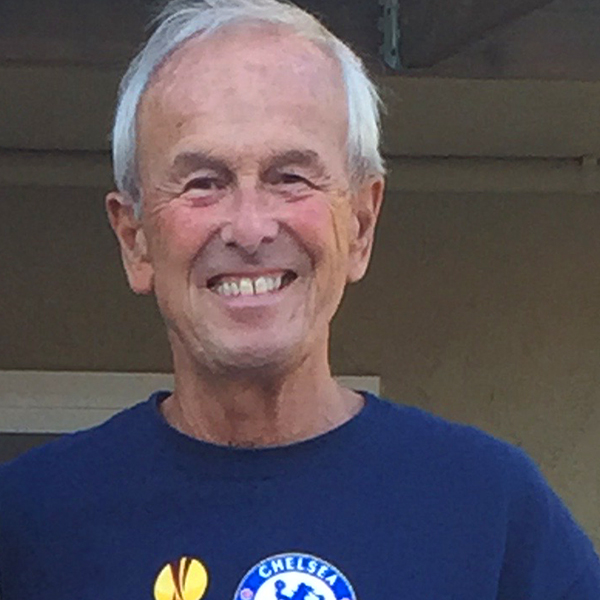
He is spearheading the Breakbulk Veterans guest author program. If you have a story to tell, contact John at [email protected].