Energy Transition, Cargo Size Pose Challenges for Providers
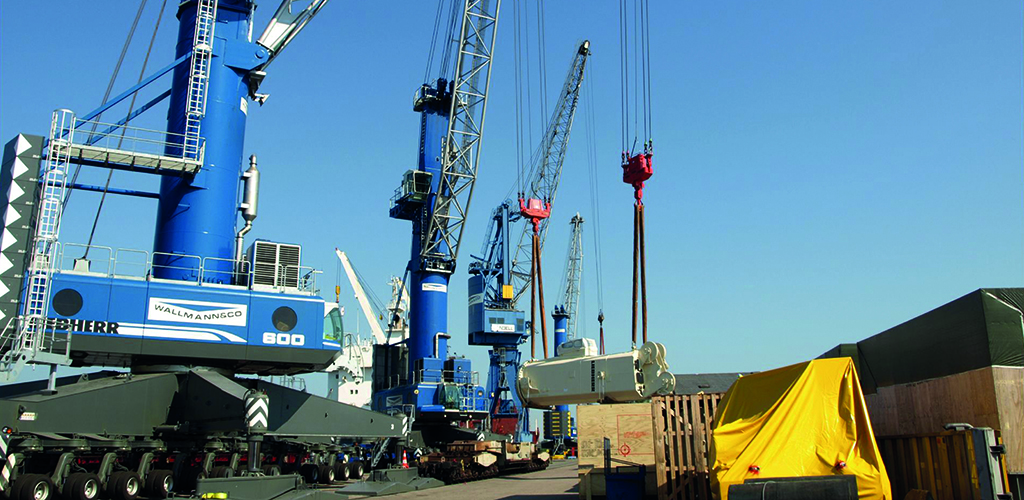
By Simon West
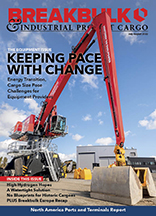
As Roger Strevens, head of sustainability at Wallenius Wilhelmsen, said at the conference: “If this is our new normal, then thank goodness for that!”
The outlook for projects in the coming years is exceptional, driven by an offshore wind sector that is expected to add a further 559 gigawatts of global capacity, or 46,000 new turbines, by the end of the decade, according to the Energy Industries Council.
But challenges persist, with port and border congestion, conflict in eastern Europe and global economic uncertainty creating headaches for companies across the supply chain, including breakbulk equipment providers.
A spokesperson for Faymonville, a manufacturer of heavy load and special transport vehicles, said sourcing of components and materials had become a challenge for production planning over the last few months, although the company could count on “reliable partners and a powerful network of suppliers to get materials on time.”
Jürgen Keller, product manager for mobile port equipment at heavy machinery maker SANY Europe, a division of the China-based SANY Group, said the whole industry faced significantly higher lead times for supply components and rising raw material costs.
The executive pointed to the congestion at Shanghai port after the recent citywide lockdown, leading to components, including vehicle transmissions, getting stuck in queues.
“These are challenges we have to muddle through,” Keller said on the sidelines of Breakbulk Europe.
Steel Supply Upended
The conflict in Ukraine is also threatening to disrupt raw material supplies.
Russia and Ukraine are among the world’s top steel producers, with facilities such as the Azovstal steelworks in Mariupol – a city in ruins following the relentless bombing campaign by Russia forces – a major regional exporter.
With uncertainty over supplies, steel prices have soared.
“It is a real problem as all the steel comes out of Ukraine,” Raymond Cron, general manager of Rezayat Logistics Group, said during an interview at Breakbulk Europe. “There is going to be a real dearth in cranes for the next few years.”
In the U.S., California-based high-capacity lift truck manufacturer Wiggins Lift said supply chain disruptions had been an issue for the industry for the last two years, coming to a head at the end of 2021 and the start of 2022.
“Increased component lead times and component scarcity has forced us to be creative with sourcing parts from different locations and be more proactive with keeping large inventories of key components on hand until parts and raw materials return to more normal availability levels,” said Micah McDowell, director of sales at Wiggins.
Longer-term challenges such as digitalization and energy transition are also having an impact, with the switch to more sustainable business practices in particular ramping up the pressure on suppliers to deliver less-polluting products for heavy-lift operations.
But there is a sense of excitement that this is an industry on the move and ready to innovate. Major milestones are being reached.
Mammoet said in April it had completed a “world-first” electric-powered heavy-lift move after deploying an electric power pack unit, or ePPU, to replace a production vessel at a petrochemical plant in the Netherlands.
The ePPU was used at the Shell facility alongside a four-axle-line self-propelled modular transporter, or SPMT, to remove an existing vessel and maneuver its replacement into position.
The operator has been working with Scheuerle, a division of Germany’s Transporter Industry International Group, or TII, on a long-term project to convert its SPMTs from diesel to renewable energy.
The ePPU is designed to lower carbon footprint and reduce emissions in built-up environments.
Mammoet and Scheuerle were unwilling to provide details on the initiative’s specific goals and timelines, but said that work remained to ensure electric power was sufficient for deployment in larger-scale SPMT projects.
“TII has been dealing with alternative drives for several years now and has already gained a lot of experience here,” a spokesperson for Scheuerle told Breakbulk. “We are working on series solutions and will offer these if the respective technology is economically viable. Until then, we will present the solution capability on a project-specific basis. The various applications are currently at different stages.”
Batteries One Solution
Battery-electric solutions will be crucial for energy transition, and although the necessary technologies are largely available on the market, they still have to be tailored for heavy-duty breakbulk operations.
“Electrification is not all news to us, most of our cranes are electrified anyway. But with mobile equipment, this is more challenging,” Keller said.
SANY itself has already launched what it said is the world’s first full-size, fully electric empty container handler, or ECH. The ECH’s 332-kwh battery gives operators a continuous working shift of eight to 10 hours, with a full recharge taking about one hour.
Energy consumption is 15 percent that of a diesel ECH, while noise is cut from 82 dBA to 66 dBA. Maintenance costs are just 25 percent of the diesel machine. According to Keller, SANY has also begun testing a fully-electric reachstacker in China and neighboring countries.
“In many areas we are moving forward with electrified solutions,” the executive said.
Another major challenge for equipment is the ever-increasing size of turbines, monopiles and other components. For haulage experts, transporting super-heavy cargo is often compounded by infrastructure flaws.
“The state of the road network in the UK is generally in a poor condition, with little maintenance or repair,” said Charlie Latham, head of tendering and business development at UK-based Allelys.
“This results in the capacity of roads and bridges being reduced. Couple this with the heavier loads being requested, and it is not hard to realize the increasing difficulties that we are having to overcome to meet our clients’ requirements.”
Future Planning Necessary
And as component size evolves, so does the equipment used to transport it.
According to Rainer Sasse, CEO at Luxembourg-based Luxtrailers, spending on equipment with a short shelf life was untenable for heavy-lift specialists using a transport leasing model.
“We need to know what’s going to be needed in five or seven or 10 years,” Sasse told listeners at a wind spotlight panel session at Breakbulk Europe.
For crane suppliers such as Liebherr, producer of the LHM 800, the world’s most powerful mobile harbor crane with a capacity to lift 600 tonnes when deployed in twin-lift operations, the constant upsizing of turbines and other components is good business.
But the growing scale and reach of cranes is creating its own challenges, especially in ports and terminals, said Andreas Ritschel, Liebherr’s deputy sales director for mobile harbor cranes.
“Mobile harbor cranes are usually the most versatile you can use in the port,” Ritschel said.
“This means many of our clients are using this crane not just for heavy-lifts, but also for bulk and container handling. But, if you design a crane which is capable of lifting 500 tonnes or 600 tonnes, it might just get too big, too heavy, too expensive to maintain and not be suitable for bulk and container anymore.”
According to Ritschel, the solution would be more dialogue between wind technology manufacturers, logistics providers and equipment manufacturers to agree on standardization of wind component sizes.
“The heavy-lift companies and others are in close contact with the wind energy producers, with the generator producers – they are in close contact. With the crane companies, nobody is talking to us. It is very tough.
“If someone could say, right, for the next ten years 800 tonnes is the maximum that we could expect for a turbine, then we would know which way to go.”
Simon West is senior reporter for Breakbulk
Photo: Breakbulk and project cargo components are getting heavier to handle. Credit: Deufol
Related Stories
Electrification Nothing New for Mantsinen
Deufol: Terminals Are Willing to Invest