May 26 | 2020
By Breakbulk Veteran Peter Jessup
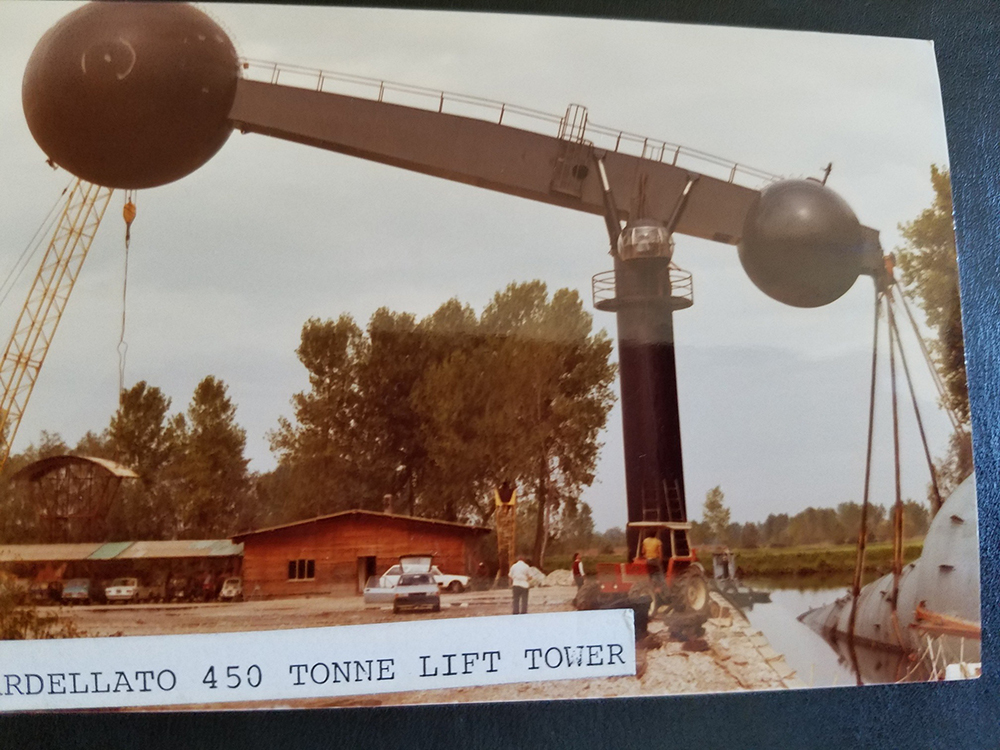
It all started when I was invited to a kick-off meeting with an Italian vessel fabrication company based in Treviso, a town north of Venice. They were supplying a reactor column for a project in the Middle East on which I was the logistics manager for a major engineering, procurement and construction company.
The weight would be 450 tonnes, dimensions were 37 meters long and a diameter of 7 meters. The delivery terms were FAS Venice. In discussing delivery FAS, I discovered they intended to place the column into a river next to their plant north of Venice, then use two small tugs to push and tow the reactor down the river and into Venice Lagoon to cross to the port. So far, so good.
The devil is in the details
However, more detailed conversation took place to get clarity on their methodology, and this created a series of significant concerns and potential problems. The tow tug would secure a chain to the main nozzle on the head of the column. When I asked if they had calculated potential loads and stress, the answer was no.
We then looked at the general arrangement (GA) drawing. I pointed out that the column had a 12-meter long skirt so it would fill with water and the head of the column was bulbous so would be full of air, and therefore it could not float level—they stated it would.
I asked had they done this before with something this big and heavy? Have you obtained authority/permits to use the river and cross the lagoon to Porto Maghera? Their response was, “This will not be a problem.”
In response to questions about details of the river, its depth, breadth and the route across the lagoon, and availability of a map showing the whole route, the answer no.
When I asked how they would lift the reactor and place it in the river, they said, “We have a dock and will use our special crane.” When I asked for details, they could not provide them.
Time to meet face-to-face
After the meeting finished, I advised the team of the problems I had identified related to the reactor delivery FAS Venice. It was agreed that I would fly to Venice to conduct a logistics survey of the river, transit across the lagoon and meet the port authorities to discuss this. Then I would visit the fabricator’s facility and review their plan in more detail.
The port authority advised they would need details of how the tow would take place, including the route through the lagoon to Porto Maghera. As I anticipated, permits would be required. They would also need the assumptions and calculations from the heavy-lift lo/lo ship owner related to the lift from the water. They provided me with a simple map of the river Sile which flowed through Treviso, then into the Adriatic.
At the weekend prior to meeting at the fabricator’s, I began the logistics survey to be more informed on the feasibility of their transportation plan. The fabricator’s facility was situated alongside the river, which was not a major river, its primary use was for pleasure boating. The facility and river were visible from the road, there was a small inlet creek between the fabricator and a vineyard. There was no dock, quayside, or crane.
My search for access
At one point as the river meandered south, a pedestrian pontoon bridge made of boats strapped together with wood planks on top crossed the river. South of this, the map identified an entry into the lagoon at Portegrandi that had lock gates. I checked them and they were only 6.6 meters wide, not enough space for the 7-meter diameter column to pass through. My search to find access to the lagoon continued.
Following the river, I passed through the town of Jesolo, a major summer holiday location with beaches on the Adriatic. There was swing bridge over the river which bisected the town. Due to the diameter of the column, it would have to be opened to allow transit on the river through Jesolo—this would need a permit.
I found a tributary branching off the river that entered the lagoon. The ability to use the tributary was essential, otherwise the reactor would have to be towed from the river mouth into the Adriatic, down the coast and then into the lagoon. Unfortunately, the tugs identified for the river tow would be inadequate for sea transportation and the alternative of using ocean tugs up river or to transfer to these downstream was unlikely.
Details of the tributary depth and breadth were not available. And to further complicate the logistics, tides from the Adriatic Sea affected both the tributary and the lagoon. Towing the column through the tributary required a high tide to ensure it did not ground on the river bed. This information was critical.
A simply extraordinary invention
I then met with the fabricator at his facility and asked him to show me the dock and crane he had mentioned during our original meeting. He took me to the inlet creek I had seen and said the dock and crane would be constructed there in time for the shipment. I pointed out that this would require a civil construction activity to ensure the dock could cope with the stress loads relating to the combined weight of the crane and column.
I was curious about this crane. He led me to a room, opened the door and presented the crane. I saw a scale model that looked like something from a Leonardo da Vinci’s sketch book! It would be a vertical cylindrical column with a cross beam on top. At each end, an orb. They would pump water from the river up into the larger orb to lift the column and then transfer the water into the smaller orb to lower the column into the creek. Always the voice of reason, I pointed out we would require the crane proof load test results.
My report was passed to our engineers who then visited the fabricator to calculate the load on the nozzle and how the column would float. Their findings were passed to our marine surveyors along with a GA drawing. The surveyors said the calculations were wrong and the column would not float level. If it did not float level, or near to level, it could be damaged and get stuck.
To every problem, a solution
Solutions to all of these risks and potential problems were as follows:
- Place a member of our team at the fabricator to liaise and validate progress on the column and crane fabrication, construction of the dock and quayside, witness testing of the proof load tests. This person would also ensure all permits were obtained.
- Engineering checked the loads on the nozzle being used as the tow connection and confirmed these were acceptable. They agreed with the marine surveyor’s recommendation to have the fabricator tack weld a plate on the base of the skirt to help it float semi-level.
- Charter the heavy-lift ship for an extra day to allow for lifting and washing the column quayside. Details of the column were provided to the owner and they undertook calculations on the lift from the sea onto the quayside and subsequent reloading onto the ship. These were reviewed by the port authorities and marine surveyor and were deemed acceptable.
- The “Da Vinci Crane” worked perfectly and the delivery went smoothly as you can see from the photo. This simple invention was used for many years by the fabricator. The two lifts by the heavy-lift ship in the port also went smoothly.
Whenever a heavy-lift cargo of abnormal size is going to be procured by your client, the EPC’s logistics team should be involved in the bid evaluation to validate the feasibility of the supplier’s proposed method of delivery. And of course, there’s no substitute for seeing it all for yourself.
About the author
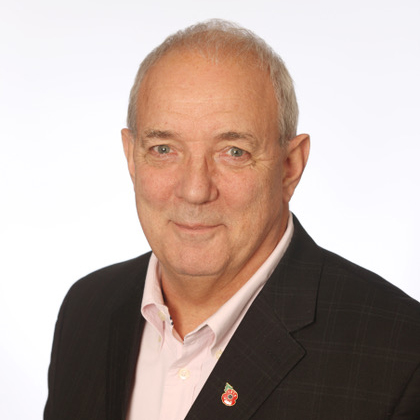
You can reach Peter Jessup by email at [email protected].
Subscribe to BreakbulkONE and receive more industry stories and updates around impact of COVID-19.