Sep 02 | 2020
A Conversation with Eric Ten Kate, Vice President of Life Sciences, Agility
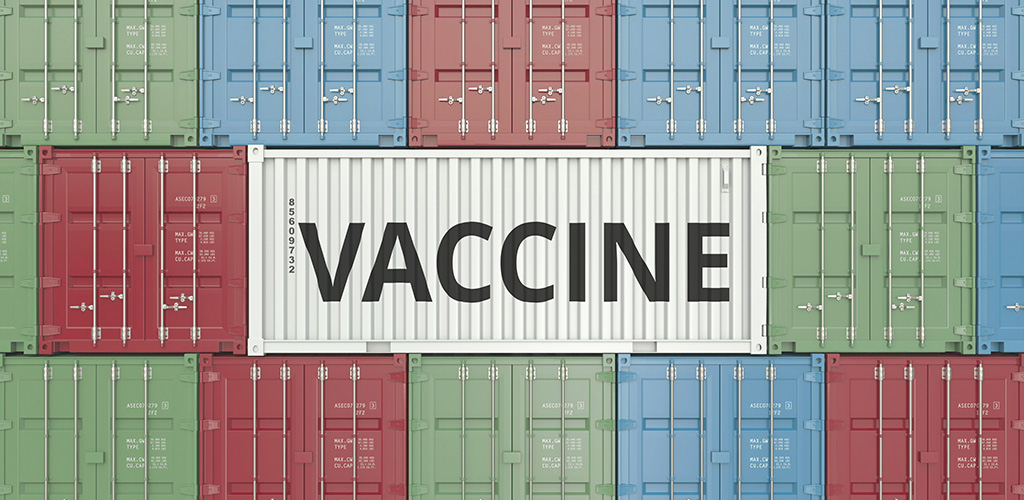
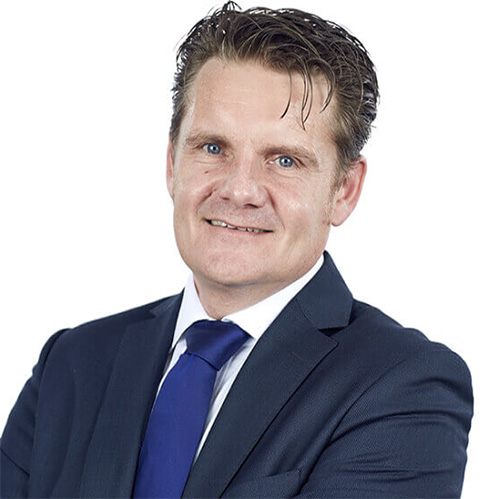
Vice President of Life Sciences, Agility
Q: Logistics and transportation companies are preparing for delivery of COVID vaccines. What are you seeing?
A: You see the whole life sciences industry at work on this, working very hard to find strategically located cold chain facilities where vaccines can be safely stored while they are awaiting onward transport or shipment to markets where they will be made available to the public. One large parcel delivery company (UPS) is opening temperature-controlled sites in Benelux countries and a massive site in the United States. We see other large shippers doing the same.
With vaccines requiring a strict temperature regime, we see an increasing demand in cold chain storage and shipping capabilities. Around the world, warehouse space is being retrofitted for cold chain. It’s a matter of adding more cold rooms where vaccines can be safely stored. For logistics providers, you ideally want cold-room capabilities near the airport, so you have easy access to uplift. Most of the doses of vaccines will be moved by air, and that’s where constraints on cold storage and air freight capacity become concerns.
Q: What temperatures are we talking about?
A: The vaccines are shipped under different temperature conditions. Ranging from 2 to 8°C, frozen (-20°C), deep frozen (-80°C) and cryo-frozen (-150°C). The safety and temperature regimen must be very, very strict. Temperature controls are less stringent for most therapeutics being used to treat COVID-19 in infected patients. The normal range for most therapeutics is 15 to 25° C, which fits relatively easily into the existing supply chain.
We are likely to have a situation where we have multiple vaccines, but each vaccine has its own temperature requirements. The active ingredients could be different from one vaccine to another, and the shipping times and distances could also vary and prompt different shipping methods. People think there is one vaccine and one set of shipping parameters and temperatures. That’s not the case.
Packaging requirements will be substantial. Local language labelling and instructions will be a challenge. That’s not as simple as it sounds. Labelling or adding expiration dates in local languages must be done according to GMP – the U.S. Food and Drug Administration’s Good Manufacturing Practices – and very few companies have GMP licenses in combination with a temperature-controlled warehouse. That gives you a feel for the complexity of this moment.
Q: What will be the biggest challenges?
A: When will a vaccine or multiple vaccines be ready? Where will they be produced? How quickly will there be deals for contract manufacturing in different regions so we won’t be overly dependent on supply chains stretched over lengthy distances for distribution? Which vaccines come first? Which work best? Which can you produce in sufficient numbers? There are a number of very good companies working on this – Moderna, Pfizer, AstraZeneca, BioNTech – to name just a few.
When you talk about moving doses in vials, you need to remember that you’ve got a very complex product requiring very specific and strict handling with more temperature-controlled packaging. Some are passive containers that are intended to preserve or maintain certain temperature ranges for a specified number of hours. Va-Q-tec, Softbox and SkyCell are a few of these providers. Then you have active containers that can be programmed at a certain temperature, such as Envirotainer, DoKaSch, and CSafe. People do not want to take risks. So the worry is that there could be a shortage of these temperature-controlled containers.
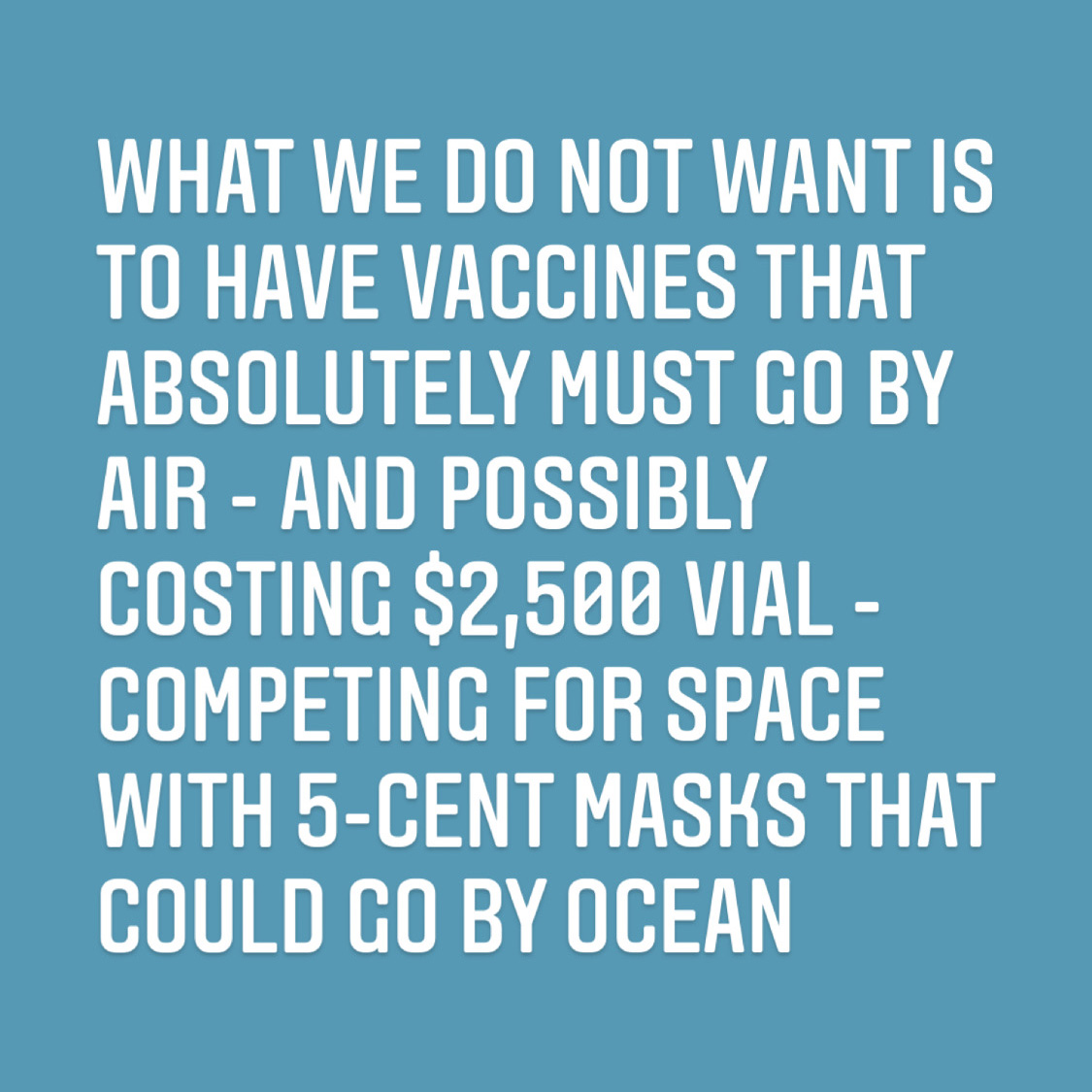
Combine this with the decline in air freight capacity due to the reduced number of passenger flights around the world, along with a renewed increase in demand for shipments of PPE globally and, of course, the normal demand for life science products. These different products all will be fighting for capacity.
What we do not want is to have vaccines that absolutely must go by air – and possibly costing $2,500 vial – competing for space with 5-cent masks that could go by ocean. More PPE is shifting to ocean, and outbound locations are shifting from China to other locations in Southeast Asia, Dubai and locally, but there are still concerns that PPE could be competing with vaccines for air freight capacity in some cases.
Q: Is there enough cold chain storage space?
A: There never is enough. Globally, we see more and more people having access to medical care and associated medication, which in turn requires more specialized storage. If I could invest my own money, I would invest in or start a warehouse with temperature control for storage of medication. You will make money on that, whether it’s in the middle of Africa or in the United States.
Q: What regions are likely to experience the most difficulty getting vaccines safely to the public?
A: Vaccines usually have a short shelf life. Manufacturers produce doses, and they are shipped immediately. Initially nobody is looking at long-term storage, they’re looking at cross-docking for quick onward movement. Normally, it would be 96 hours from factory to patient. Ninety-six hours might even be long in the early going. Everything being produced is going to be consumed right away. The vaccines in trials are being used immediately. So this product is not going to sit on the shelf for very long.
Getting vaccines to the public will be difficult in Africa, we know. It’s more problematic because there’s hardly any cold storage at airports in Africa. The World Health Organization and UNICEF and the Gates Foundation and USAID and others are going to have to be involved in that. They are aware that this is a problem. People are starting to understand that we need to build things up, predominantly in Africa, to be able to handle it.
The US, some European countries and other wealthier nations have signed agreements with drug companies for early access to successful vaccines. The upside of that is that the drug companies secured much-needed financing to pay for vaccine development. The other side is that poorer countries could find themselves at the end of the line when it comes to access.
Vaccines are normally produced in batches of 100,000 to 150,000 doses – vials or syringes – a day. That sounds like a big number, but it’s not when you are talking about the global need for up to 8 billion doses.
Once vaccines become more common and available, like a flu shot, the situation will be something different. At that point, you might have in-country storage of products with an extended shelf life if you have governments and health ministries building safety stocks.
Q: What role will cold chain tracking and IoT play?
A: From a risk mitigation perspective, tracking and tracing and IoT will play an important part. It is vital that we ensure product security throughout the entire supply chain. Not only in terms of establishing and using validated temperature-controlled transport and storage solutions, but also in terms of managing risks such as product integrity and risk of theft since these vaccines are transported across the globe.
You have requirements for serialization – barcodes or QR codes for each individual product. You need to be able to scan the code and find out where exactly it was made, and have full traceability. With these high-value goods, this is the rule rather than the exception. You need to trace it all the way from factory into the patient so you know who got what dose and from what batch.
Can our current serialization infrastructure actually handle that? It’s not a globally deployed system. We haven’t had to assemble and store that much data before – we’re talking about billions of doses and up to 8 billion individuals who could receive a vaccine. You’re tracking active ingredients. You’re tracking vials, syringes, needles, labels, caps and other packaging materials. Then you’ve got to track doses, batches, containers, and temperature data. We haven’t seen anything this massive before.
Useful Resources from Agility
- Map of countries that have closed borders due to COVID-19
- Global Map from John Hopkins (Interactive maps show cumulative cases, active cases, incidence rate, case-fatality ratio, testing rate)
- Coronavirus Outbreak – Impact on Shipping (Nepia)
Subscribe to BreakbulkONE and receive more industry stories and updates around impact of COVID-19.