Aug 19 | 2021
Breakbulk Supports UAE’s First Nationwide Rail Project
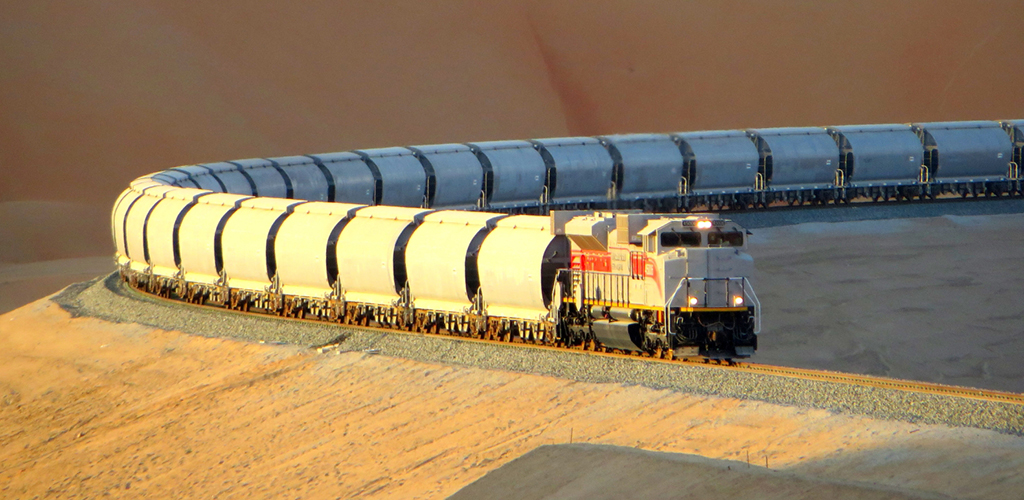
This story is preview content from Breakbulk Issue 5 / 2021, to be distributed Friday, Sept. 9 and at Breakbulk Americas
By Simon West
A heavy-haul locomotive pulling more than a hundred 30-tonne hopper wagons loaded with granulated sulfur cuts through the desert dunes of Rub’ al Khali in the United Arab Emirates.
The convoy, stretching for almost two kilometers, is transporting the sulfur – a byproduct of the Abu Dhabi National Oil Co.’s natural gas operations at Shah and Habshan – to the Port of Ruwais on the UAE’s Middle East Gulf coast for processing and export.
The initial stage of the UAE’s first national rail network began operations in 2016. Since then the 264-kilometer line linking the Shah and Habshan fields with Ruwais has delivered almost 40 million tonnes of granules for ADNOC, with two trains shifting a combined 22,000 tonnes per day.
The project, developed by Etihad Rail, is now entering its crucial second stage, a 605-kilometer route connecting all seven emirates from the town of Ghuweifat on the Saudi border to Fujairah on the Gulf of Oman coast via Abu Dhabi, Dubai, Sharjah and Ras al Khaimah.
The network is expected to help the UAE diversify its oil-dependent economy and support its green ambitions by cutting CO2 transmissions from road transport by up to 80 percent.
Planned expansions into Abu Dhabi’s desert interior would stretch the route to 1,200 kilometers, while the terminal at Ghuweifat would link to the rest of the Gulf Cooperation Council, or GCC, in a proposed region-wide rail system.
“The advantage of the railway for them is that it is able to haul big quantities of natural resources,” said Kevin Smith, editor-in-chief at the International Rail Journal. “Extracting the mineral wealth and transporting it out of the country – the most efficient way to do that is by rail, especially from the interior where the environment is a lot more hostile.”
Staged Development
Etihad Rail has divided the second stage into four so-called packages. Package A, a 139-kilometer line from Ghuweifat to Ruwais, is being built by a joint venture between China State Construction Engineering Corp. and South Korea’s SK Engineering and Construction. Track-laying for the route began in January, with local heavy-lift specialist Al Faris hired to shift the first shipment of rails.
The Dubai-based company used custom-built flatbed trailers to carry the 25-meter-long rails 250 kilometers from the Port of Mina Zayed in Abu Dhabi to Etihad Rail’s laydown zone at Ghiyathi. Some 12,000 tonnes of track were hauled through the desert in 250 separate trips over 26 days.
The forwarder was also recruited this year to deliver seven of 38 locomotives earmarked for second-stage operations. The 138-tonne engines, designed and built by U.S.-based Progressive Rail and fitted with special filtration systems to keep sand out of the components, were carried in one overnight convoy using Goldhofer Transport THP mechanical trailers.
Other heavy items requiring breakbulk support include earthmoving equipment, track-laying engines and freight wagons, which are expected to number more than 1,000 once the network is fully operational. Some 842 wagons boasting four different capacities are being designed, built and delivered by China’s CRRC Yangtze, according to Etihad Rail.
Packages B and C linking Abu Dhabi’s Khalifa Port and Khalifa Industrial Zone with Dubai’s Jebel Ali Port, the Middle East’s busiest shipping destination, were awarded to China Railway Construction Corp., or CRCC, and Abu Dhabi-based Ghantoot Transport and General Contracting Co.
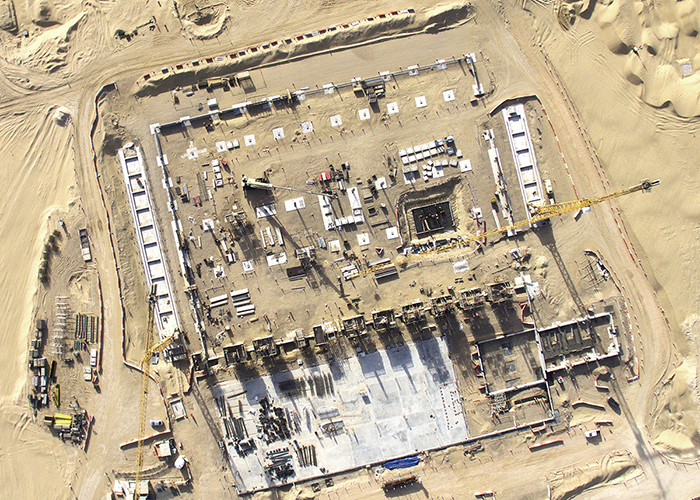
An operations and maintenance facility at Al Faya is partially complete, while a purpose-built, 9,000-square-meter factory at Saih Shuaib has a capacity to churn out 3,200 pre-stressed concrete sleepers per day. The 2.6-meter-long, 340-kilo sleepers are made from cement and aggregates sourced from quarries in the northernmost emirate of Ras Al Khaimah.
“Engineering-wise, building a railway in the desert is easy in the sense that there are no buildings in the way, but difficult in that it is quite a hostile environment with high temperatures and moving sand dunes,” Smith said. “There are a lot of things you have to do on a desert railway that you do not have to do on a conventional railway to protect the infrastructure.”
An ‘Aggressive Timeline’
Installing the first stage of Etihad Rail, which was carried out simultaneously with the construction of the Shah gas plant and a ship-loading facility at Ruwais – as well as upgrades at Habshan – was no mean feat.
More than 4,000 workers and 30 subcontractors took less than three years to complete the line. The excavation of more than 90 million cubic meters of earth and the installation of civil works, tracks and systems were carried out by lead contractor Saipem, an Italian firm operating in the energy and infrastructure sectors, alongside partners Tecnimont and UAE-based Dodsal.
“The project was delivered under a very challenging and aggressive timeline, with key dates based on the two sulfur producing plants and the ship-loading facility all coming on stream,” a Saipem executive involved in the project told Breakbulk.
“Specific training was provided for desert working conditions, such as driving in sand and recognizing and combating dehydration and heat stroke. Other training highlighted the risks from snake bites during the summer.”
Minimizing the environmental impact of the project was also a top priority, with the contractors working closely with Abu Dhabi’s environment agency to safeguard protected forests and animal habitats.
“Bridge crossings and reinstatements of tracks were extensively carried out using underpasses and overpasses, special camel crossings were provided every seven kilometers, reptile crossings were also provided and wadi crossings for seasonal hydrological events were included,” the executive said.
The second stage, which could eventually be tailored for passengers, poses even greater tests for contractors.
Excavation work through the Hajar mountains for example is demanding “softer” blasting techniques to ensure stability and to protect biodiversity, while integrating the network with the UAE’s ports is a major challenge.
Roger Clasquin, CEO of RAK Ports, a chain of ports located in Ras Al Khaimah, said rerouting internal traffic in existing terminals to accommodate rail hubs would require significant investment in bridges, tunnels and other costly infrastructure.
“Discussions (on integration) are still ongoing,” the CEO said. “In Fujairah the rail will end up inside the port. In other locations it will make more sense to have a railway siding where the cargoes are being produced and received so it does not necessarily have to be at the port.”
Contacted by Breakbulk, Etihad Rail was unable to provide a timeline for the second stage, although previous projections had completion slated for 2024.
In statements, the developer said the fully functioning network would shift close to 60 million tonnes per year of containerized and bulk freight, including petrochemicals, aggregates, construction related materials, industrial and perishable goods, waste and cement.
Bringing in Contractors
Freight contracts between Etihad Rail and producers are already being signed off.
In April, mining company Stevin Rock signed a deal with the developer to transport raw materials from Ras al Khaimah to Abu Dhabi for use in the construction, cement, steel, mining, glass and chemical industries. Some 3.5 million tonnes will be shipped from Stevin Rock’s Al Ghail quarry in 500 annual trips, according to a release.
Meanwhile, neither Etihad Rail nor the UAE’s federal transport authority could provide an update on plans to connect the six members of the GCC – the UAE, Saudi Arabia, Qatar, Oman, Bahrain and Kuwait – in a region-wide rail system. The 2,177-kilometer Gulf Railway has hit several stumbling blocks since being approved by member states at a 2009 summit.
“The broader GCC rail network project has faced delays for multiple reasons, some based on fiscal restraint since 2015 and some on basic regional integration problems of a more political nature,” said Karen Young, a senior fellow at the Washington, DC-based Middle East Institute. “There are more efforts on a national basis to develop new logistics and transport projects. How these connect and create synergies for the region is less clear.”
Linking the UAE to the rest of the GCC would be relatively straightforward, with national networks, tracks and systems in the region in line with U.S. and European standards, according to Smith.
“It is not a case where one of the countries is very different to the other and that will cause interoperability issues. They are on the same page of what they are building, so you will be able to run cross-border,” Smith said.
A green light for such an ambitious project would be a boon for breakbulk. According to Shashi Shekhar, chairman at the Dubai-headquartered Supply Chain and Logistics Group, cargo-carrying opportunities linked to a GCC train network could be worth in the region of US$30 billion to US$40 billion.
“Investment in railway infrastructure is for sure creating big transport and logistics opportunities for the heavy-lift and movement industry,” Shekhar said.
Colombia-based Simon West is a freelance journalist specializing in energy and biofuels news and market movements in the Americas.
Photo Credits:
(Lead image) The initial stage of the UAE's first nbational rail network began operations in 2016. Since then the 264-kilometer line linking the Shah and Habshan fields with Ruwais has delivered nearly 40 million tonnes of granules for ADNOC. CREDIT: SAIPEM.
(Image in story) The Operations and Maintenance facility at Al Faya will be the largest and most significant on the network. CREDIT: ETIHAD RAIL.