Jan 03 | 2024
New Regulations Raise Redesign Questions
_1.jpg)
From Issue 1, 2024 of Breakbulk Magazine.
The new European Machinery Regulation has passed all political hurdles and is due to come into force in 2027. The result is that more than 860 European norms and standards will have to be rewritten and harmonized to align with the regulation – and the impact on Europe’s heavy-lift sector will be profound.
There isn’t enough time to do all that work, especially because the guidelines around interpretation to accompany the Regulation are yet to be completed, says ESTA, the European association for the abnormal road transport and mobile crane rental sectors.
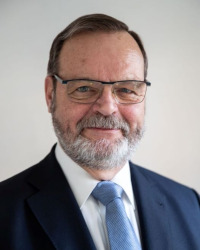
However, of more concern than the time constraints, the heavy-lift industry has flagged up two specific sections covering requirements relating to overhead power lines and protection against corruption.
According to ESTA, manufacturers have repeatedly pointed out that building the required safeguards relating to power lines into the design and manufacture of equipment is technically impossible, but despite these concerns the regulations were published largely unchanged.
“There was consultation – but they don’t necessarily listen to what you say,” Klijn said. “Manufacturers, especially on the topic of power lines, are looking for some amendments. Until then, they will have to do their best. ESTA is pushing as hard as we can to get an amendment before the deadline.”
It is “so obvious” that the present text won’t work, Klijn said. He predicted that until changes are made, the value of second-hand cranes will go up because these are not affected by the new regulations.
Describing the regulations as “wishful thinking”, he said: “If manufacturers abide by the letter of the regulation, they can’t manufacture cranes anymore.”
Confusion and Conflicts
The regulations state that all mobile machinery such as mobile cranes and access platforms should ‘where relevant’ be designed to prevent contact with overhead power lines or where the risk cannot be avoided, designed to ensure that all hazards ‘of an electrical nature’ are prevented.
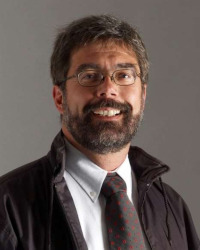
“Having the requirements in the Machinery Regulation means the European Commission thinks we have the means to solve a problem in a technical way, so it doesn’t come into the domain of the user. Of course, this is the case in many of the requirements. If you prevent something from being overloaded, then it can’t be overloaded. If you design equipment so it can’t tip over, then it can’t tip over, irrespective of what the person does with the equipment. So, you should follow the TOP principle. But what if physics stands between you and a solution? This is the situation we have with this ‘contact with power lines’ topic.
“This is a Machinery Regulation, but they are only talking about the operator,” Meissner said. “In real life, if you have contact to a power line, then the operator and other people in the vicinity are in danger.”
It must be understood that a power line may or may not have a current flowing through it, he said. A high-voltage line might have no current flowing, so one cannot sense for electromagnetic fields; but if a piece of equipment makes contact, then the current will flow and it is too late to sense the electromagnetic fields.
“We would have to sense for electrostatic fields, which are much weaker and can easily be influenced by the presence of metallic parts, for example.”
Sensors for Safety
There are products on the market which claim to be able to detect electrostatic fields, but the measured results of these sensors are not as reliable as needed for a safety device, Meissner said, “When you look at the manuals for these pieces of equipment, you find information that the device may not serve as a safety device. The sensitivity must be adjusted by the operator – so in the TOP pyramid you are back at the bottom,” Meissner said.
Klijn added: “The EC is saying that there are all sorts of systems that will prevent equipment hitting power lines – but the instruction manuals for these systems say you should stay 20 meters away because you can’t rely on it.”
If job sites are managed properly, people should be addressing the risks correctly, Meissner said. “First, analyze if there is a power line in the vicinity of your project. If not, no problem. If there is, talk to the power line operator, ask if it is energized and at what level, and ask if they could shut down the line for a period of time. If not, plan your job so that you always maintain a certain distance and have people checking you do this. As long as this current practice is properly observed, nothing happens.”
He also criticized the stipulation that if contact could not be avoided, every electrical hazard must be prevented. “This is the second piece of nonsense. What is every electrical hazard? A current can go through a crane and the tires can burn, ignite the hydraulics and everything is on fire. Can a control system on equipment decide what is the right action? No, the operator in the equipment must decide.”
There are no devices in today’s market that can warn the operator and protect the equipment from power lines transmitting a broad variation of electrical power, said Peter van Oostrom, global projects assets director of Mammoet. “The most logical solution available today to mitigate this is to perform thorough risk analyses and job planning, working closely with the power line companies to eliminate the power, and maintain a safe distance.”
However, he added: “On top of this, the crane’s electronics can support the operator, using the working range limiter functions on the machines, where a digital spotter stops crane motions at a set point to stay clear from the danger.”
The majority of the Mammoet crane fleet is purchased or built in Europe, van Oostrom said. “The equipment manufacturers have a significant task to fulfill the requirement related to overhead power lines. Mammoet is a member of the CEN/ EN 147/WG11 – Standard of Mobile Cranes EN13000, where this topic is giving a lot of discussion.”
Update Welcomed
The new Machinery Regulation is replacing the old Machinery Directive 2006; an update is welcome to be more up to date with today’s developments, van Oostrom said. “Both are broad, but the impact is different. Being or staying compliant has some challenges where we could use the Machinery Directive including norms and standards.
With the new Machinery Regulation in place, the standards are not reviewed and updated yet. This means we need focus to ensure we fulfill both the Machinery Regulation and standards to maintain compliance. “With the Machinery Directive there was a manual that gave more details per topic mentioned but the new Machinery Regulation does not have such a document yet. We believe that for completeness, this is much needed to explain the background and use of some regulations.”
A section on corruption in the new regulations also needs clarification, according to ESTA. This states that any interface to the machine must be protected against corruption. This, said Meissner, is intended to protect against hackers taking over a machine and operating it in an unsafe or unintended way.
“Unfortunately, they have written this chapter in a way that it is understood that any interface is to be protected – for example, the hydraulic interface, air, electric interfaces, etc. This has led to discussions where some truck manufacturers feel they could be liable if someone misuses interfaces, such as when refilling tires. Of course, we have to protect against sabotage but people with bad intentions will always find a way into those systems.”
ESTA’s Klijn said: “The so-called protection against corruption means you have to safeguard your machine from being corrupted from outside – especially with the number of electronic interfaces. The EC doesn’t want someone in China hacking and taking over your digger. From a technical point of view, most machines can be influenced remotely. This is something the EC thinks we should safeguard ourselves from, but it is not easy to do.
“You might also have to protect your hydraulics – how do you protect your hydraulic hose from someone cutting it? People who have written these regulations are on a high abstract level and don’t really have a connection with the ground as to how this might work out in practice.”
Connecting Theory with Reality
Safe equipment and safe equipment handling are very important, van Oostrom said, but it is so important to connect theory with reality. “In the real outside world, fulfilling these theories in equipment could result in redesigning equipment with some technical and probably also financial impact. For Mammoet, where we use our own designs for fabrication or assemblies of equipment, we need to review these before they can be reused again in new assemblies.”
However, he concluded: “Fulfilling designs to the standard required by the new Machinery Regulation is not a goal in itself. It is the basis for safe design of machines. On top of the regulation, other standards have to be used like ISO, EN, and so on, which have an impact on all the parts and components you buy to be compliant. It is the assembly that is a challenge. The assembler of the final product is responsible in Europe for the CE declaration – meeting all requirements.”
Felicity Landon is an award-winning freelance journalist specializing in the ports, shipping, transport, and logistics sectors.
MAIN PHOTO: Liebherr ecol mobile crane operator. CREDIT: Liebherr