Jul 13 | 2023
Seminal Project Ten-plus Years in the Making
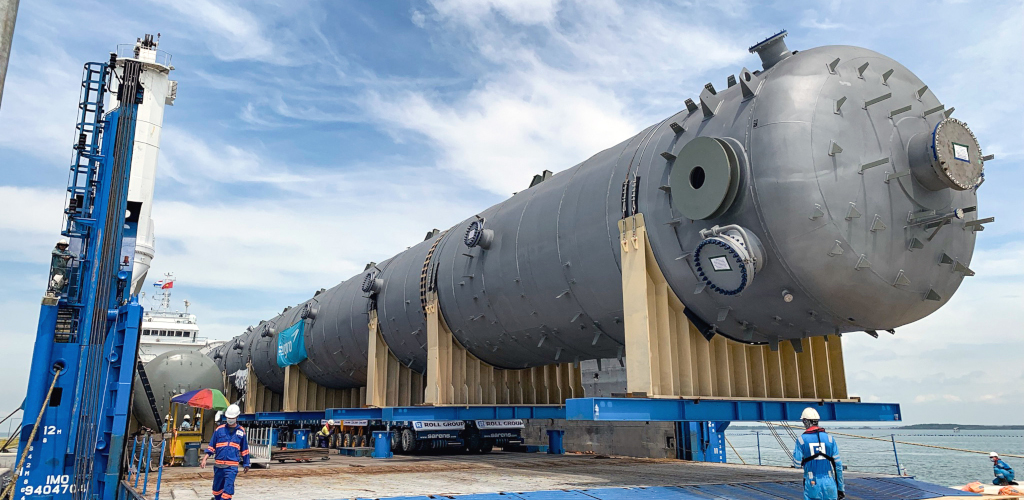
By Malcolm Ramsay
In a case study from Issue 4 of Breakbulk Magazine, we look at how deugro overcame remote working, under-strength quays, rocketing rates and other challenges to move an incredible 280,000 freight tons of cargo for a petrochemical project in Vietnam.
When it comes to demonstrating the power of meticulous planning, global coordination, and innovative problem-solving in the breakbulk industry, few projects stand out like the Long Son A1 – Olefins Plant Project in Vietnam. The scale and complexity of the undertaking, conducted amid an array of unpredictable challenges, including the Covid-19 pandemic, have set new standards for what can be achieved in the sector.
For this project, freight forwarding specialist deugro was tasked with the timely shipment and delivery of 280,000 freight tons of petrochemical equipment from over 35 seaports and airports around the world to the construction site on Long Son Island near Vũng Tàu, Vietnam.
This vast cargo included 178,300 freight tons of critical oversized and heavy-lift components, including a behemoth C3 tower, weighing a colossal 778.1 metric tons and stretching almost 100 meters in length. In total, 155 separate breakbulk shipments were delivered over the course of the project, utilizing 55 chartered heavy-lift vessels.
The successful completion of the project this year is the culmination of plans stretching back over a decade.
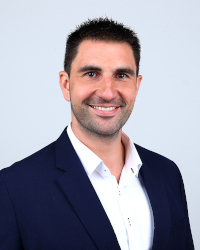
“The project started to gain momentum in 2017, after being on hold since 2009,” Benjamin Mutti, regional director, deugro Singapore & Malaysia, told Breakbulk. “deugro Singapore, together with deugro Vietnam, closely monitored the developments of the project, and in February 2018, deugro conducted an initial route survey for TechnipFMC on Long Son Island and the nearby port,” the executive said.
Being one of TechnipFMC’s approved project freight forwarders, deugro was strategically positioned and its experience, coupled with its well-established office setup in Vietnam, proved vital. By August 2018, TechnipFMC had clinched the award for the project, opening the way for preliminary budgetary inquiries and shipments.
With the wheels in motion, the main tender was released in early 2019, leading deugro Singapore to secure the offshore award and deugro Vietnam to receive the onshore award by Christmas time that year.
Close Coordination a Necessity
Given the magnitude of the petrochemical plant and the diverse array of origin countries for cargo, a high degree of coordination was required from the start. Components were required from over 15 countries, and this entailed an intricate dance of logistics and planning, with teams coordinating across multiple time zones.
“Ensuring the on-time shipment and delivery of over 1,400 breakbulk, container and air freight shipments was challenging,” Mutti noted. “And to ensure the required sequences of the construction site, timing, flexibility, and daily status reports demanded a high level of communication and coordination with all parties.”
Having finally got the project started at the tail-end of 2019, the teams then faced a massive curveball in the form of the Covid-19 pandemic. A few short months into the planning process the world was locked down, with widespread and ever-changing restrictions put in place at short notice, significantly impacting shipping and delivery schedules.
This necessitated frequent, sometimes daily, changes to the schedule, which had to be integrated into the project plan. Yet through a combination of adaptability, clear communication, and swift decision-making, the team navigated these unanticipated waters in the early days of 2020.
In total, deugro Singapore, as the project control hub, worked closely with 16 deugro country organizations around the globe, connecting more than 50 deugro experts with client and subcontractors daily to ensure up-to-the-minute status updates.
Collaboration With Carrier
Early in the project’s lifecycle, deugro and dteq teams identified the size of the largest components as challenges when transiting key chokepoints, with the hefty size and weight of the main cargo pieces, such as the 338-metricton C2 tower and the 600-metric-ton quench water tower, presenting significant logistical hurdles.
“More than 70 comprehensive method statements had to be prepared for the safe movement of the cargo components across all interfaces,” Mutti said. “To ensure cargo movement, loading and stowage processes in accordance with the highest safety requirements, there were detailed route surveys, motion response analyses, ballasting and mooring calculations, ramp arrangements, lifting and rigging calculations, as well as stowage and sea-fastening designs.”
To streamline this process, deugro and Roll Group built on the close partnership already developed between the two firms on previous projects and began devising a solution that was both pioneering and safe, ensuring the successful navigation of the cargo between the vessel cranes.
“deugro worked with the experienced teams from dteq Transport Engineering Solutions and Roll Group, whose experts conducted route surveys, identified obstacles and developed technical solutions during personal on-site visits in Malaysia and Vietnam over a period of several weeks,” Mutti said. “They prepared route surveys, designed lifting, rigging, stowage and cargo securing plans, calculated ramp arrangements and drafted loading and discharge plans.”
The initial plan was to use roll-on, roll-off operations for the larger pieces of cargo. However, the combined expertise of the partners led to the creation of a more efficient solution. Instead, the teams redesigned the early lifting plans and found a way to safely lift the quench water tower and the C2 tower. This included the temporary removal of a crane boom support, a clever adaptation that made room for the large units and not only ensured the safety and integrity of the cargo, but also saved the client time and costs.
Robin Koenis, managing director Asia Pacific at Roll Group, highlighted the importance of clear timescales for successful execution, noting the need for sufficient time to fix vessels and equipment and to setup and align the land and sea engineering scope. “The early involvement of the land and sea carrier to align fabrication supports and grillage and sea fastening on the ship, as well as the SPMT trailer configurations on both sides was vital,” he said.
Foreseeing the skyrocketing global freight rates, deugro also proactively contracted six semi-submersible, heavy-lift multipurpose cargo vessels, providing a guarantee of cargo space and some stability on project budget.
Choregraphing Complexity
With pre-planning out of the way, the next major stage of the operation was the pre-carriage of the largest breakbulk components from the production yard of KNM Process Systems in the Gebeng industrial area, Kuantan, Malaysia. This included the giant C3 tower, which had to travel six kilometers to the nearby Kuantan Port on Malaysia’s east coast.
“To roll the cargo onto the vessel was not an easy task. It took months of planning and careful calculations by a team of professionals from Kuantan Port, Roll Group, Worldwide and KNM, among others,” a spokesperson for Kuantan Port explained.
For the safe transportation of the C3 tower from the production yard to Kuantan Port, a journey management plan, including traffic and road diversion, was designed and approved by the port prior to the start of the operations. Safety analysis meetings were then held to ensure emergency routes and access for emergency vehicles and to inform the public about waiting times and road closures.
Mutti explained that the main challenges were “obstacles at the fabrication yard, tight turning radiuses, and inadequate ground-bearing capacities on the road and especially at the port – resulting in countless axles being added to distribute the load better. Therefore, additional trailers from the U.S. had to be shipped in to meet these exceptional requirements.”
Further preparations included the removal of lamp posts, the arrangement of permits and police escorts, levelling and compacting pinch-points, power and telephone cable lifting, strengthening of drains, as well as trailer performance checks and daily equipment maintenance.
This operation was made more difficult by the tight space at the dock and the team from Kuantan Port noted that “to position the cargo parallel to the vessel, the ground team had to turn the cargo 90-degrees in a very limited space. Then they had to wait for hours until the sea tide was at the desired level to roll the cargo onto the vessel. The overall operation took 6 hours to complete.”
To ensure the safety of this maneuver, the ground had been reinforced with almost a hundred ramps and steel plates placed to achieve a load spreading sufficient to meet the port’s ground-bearing capacity of 3 metric tons per square meter. Even with this precaution, the concrete curb at the jetty had to be removed and rebuilt, and then repaired after the operation was completed.
“The biggest challenge was coordinating with the relevant authorities to ensure smooth and timely operations from fabrication yard to site, while adhering to strict Covid restrictions,” Koenis of Roll Group added.
Loading Operations Underway
After the arrival of the ocean vessels, the components were loaded aboard with additional sea-fastening requiring various welding and lashing work. To safely secure the C3 tower on the turntables, additional “d” rings had to be welded to the trailer and the cargo to be able to secure it properly.
“The most challenging units were the 600-metric-ton quench water tower, which required two 36-axle lines to be driven alongside the vessel, and the C3 tower, which required two 48-axle lines,” Mutti said. “Comprehensive method statements for the operations were based on detailed motion response analyses, ballasting and mooring calculations, ramp arrangements, lifting and rigging calculations, as well as stowage and sea-fastening designs.”
Prior to each loading, meetings and toolbox talks were held with the vessel’s master, the cargo superintendent, the marine warranty surveyor and the client’s representative, as well as all persons involved, to minimize any risks.
All units, except the C3 tower, were loaded by vessel crane in tandem lift operations at the main berth, although some units, such as the C2 tower and the quench water tower, caused additional challenges since they nearly reached the vessel crane’s lifting capacity and the space was tight between the cranes to swing the cargo on board.
As Kuantan Port had never conducted a roll-on, roll-off operation before there was a steep learning curve for some staff, but meticulous preparation and clear communication ensured each operation proceeded without incident.
“The chance to handle such an unusual and delicate operation was a meaningful experience for the staff of Kuantan Port,” the port authority’s spokesperson said. “We are honored and glad to get everyone involved connected to this golden opportunity.”
Overcoming Discharge Hurdles
After the secure arrival at the Phu My construction jetty in Vietnam, the components began their discharge phase. This was a well-orchestrated process that utilized both roll-on, roll-off and lift-on, lift-off operations. Notably, Phu My port’s ground-bearing capacity stood at an impressive 10 metric tons per square meter, significantly higher than that of Kuantan Port, making the discharge process somewhat less complicated as it reduced the need for as many steel plates and axle lines.
Despite this, there were still some obstacles. As Mutti described: “One of the biggest challenges was the turn from the jetty to the road at the job site, which was overcome through detailed planning and the correct use of axle lines… to safely roll off the C3 tower, several fenders had to be removed to allow the vessel to move closer to the jetty for positioning the ramp.”
Once cleared through customs, the cargo began its final journey along a 1-kilometer heavy haul road to the site’s dress-up area, utilizing 64 axle lines across self-propelled modular trailers and traditional trailers. The sheer size and weight of the C3 tower, alongside restrictions imposed by the trailer setup and the terrain, demanded thorough preparation and engineering.
“The area in and around one pipe rack on the construction site was extremely tight, so it took several meetings, site inspections and engineering sessions to identify a safe travel path,” Mutti said. “The road around the pipe rack had to be compacted and levelled to ensure the turning radius was fully utilized.”
As it was the rainy season by this time, many areas were completely under water, and sand and soil had to be piled up. As a result, deugro’s teams arranged for pumps and drainage to remove the water and dry out the area. Despite these challenges, however, all components were safely delivered to the site, on time and in good order, even amid the challenges of Covid-19 restrictions.
Christophe Reveilloux, head of transport operations at Technip Energies, praised both deugro Singapore and deugro Vietnam for their professionalism, highlighting the hard work put in by all partners in getting this ambitious project over the line.
“While it seemed impossible at first, a project can be managed remotely if you have the right people on the ground,” Mutti concluded. “Early engagement with the right partners was the key to success. deugro brought the teams of TechnipFMC, deugro, dteq, and the heavy-lift partners together at an early stage, and this made it possible to engineer solutions around the many challenges we were facing and keep to the client’s project schedule.”
MAIN PHOTO: Maneuvering the nearly 100-meter C3 tower on the project construction jetty in Phu My Port, Vietnam. CREDIT: deugro