Dec 05 | 2023
How Contingency Planning Gives Your Company a Competitive Edge
.jpg)
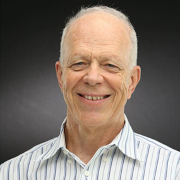_2.png?width=170&height=170)
We finished the articles on TOC with the question of how to proceed if the TOC for alternative routes gave more than one which had very similar values. The question then is more than an economic one; other aspects need to be considered, which brings us to Risk and Resilience that can be used to make a measured and rational decision.
Part of any responsible logistics organization is to ensure that goods are delivered to the end customer at the right time and at the right place. It is a foolish logistics manager who believes that operations will not be affected by the external environment, and everything will continue to operate as it does today. That is extreme hubris, and is often reported in the press as “supply chain issues”, where production is delayed, or customers let down because something in the environment altered. This is particularly true for organizations that have looked at the supply chain as a source of cost savings only and have driven the logistics chain to be lean to the point where there is no safety stock to cater for issues.
Risk is inherent in all we do in business. We cannot see everything clearly as if we had a crystal ball, so the aspect of risk remains for all operations and needs to be part of the strategy. At a strategic level we need to look at risk and plan for it. Operationally these plans need to be sufficiently wide and detailed to enable the organization to adapt quickly to match the exact event details and then implement. Companies that only plan during an event are more likely to fail, and only the strong and prepared survive. Thus, planning with multiple parties present, documenting the way forward in proposed scenarios and having these documents simply presented is essential.
And every organization must have the information flow for events brought to the decision-making point or points of logistics, so that the events are identified quickly, or preferably forecast as data, which show there are changes occurring, and planning to cope with these changes is in place. While all decisions should be made using economic information and calculations such as the Total Cost of Ownership, when there are two choices with similar economic value, risk becomes the deciding factor.
Risk and Resilience in a Logistics Chain
Risk and Resilience are two parts of any strategy. Risk is what might cause delays or disruptions. Resilience occurs in two parts. The first is actions such as the deliberate choice of multiple Logistics Service Providers (LSPs) so that a failure or problem with one is not a major concern to the shipping of the goods. This spreads the risk of the operations. The second is to identify the risks and plan for the minimization of these identified risks which are not in the control of the company. Resilience is built into the logistics chain by spreading the risk, getting early warning and planned actions to minimize the consequences of the risks so that they are not major. The resilience of a logistics chain is defined by its capability to resist the impact of the risks it faces and its speed of recovery.
One can break down the risk into four broad categories which cover all the eventualities that need to be considered:
• Technical and Infrastructure
• Socio-political
• Natural
• Operations
These need to be considered in terms of logistics issues that might affect a company and its ability to service its customers.
Resilience
Resilience in the logistics capability of an organization is a strategic source of advantage. It becomes evident only when there are issues with the movement of the goods which are extreme, but the strategic element is that the world class logistics capability will have planned for the type of issue, and to have plans in place which allow it to respond faster and more successfully than its competitors.
The strategy for a logistics organization, which aspires to be world-class, must include a review of where the organization is to perform its work, and what are the problems that could be encountered. While we have shown that there are four major categories of risk, the actual risks as seen by the organization need to be identified and defined as to the impact on the organization. The method to achieve this is to have teams comprised of personnel who are involved and knowledgeable of the movements and risks. They need to agree in a structured manner which risks are not within their control and what the impact would be if they occur. Once identified the response to that type of risk must be planned for. This planning must be in a simple format that the organization can use if such an issue arises, and not require two days of reading to assimilate.
Business history has many companies which have foundered due to an issue that would be hard to foresee without this strategic planning for resilience. The case of Nokia and Erikson, the mobile phone producers, will illustrate this simply. Chips for many cellular phones were made in a special fabrication facility which has ultra clean standards. The fabrication facility suffered a lightning strike, and the resultant fire damaged the facility. Nokia senior management had a plan in place and personally contacted the owners of the fabrication facility. They offered help to bring it back online including technical personnel to assist. Erikson waited so the fabrication company could contact them and let them know what had happened and when they would return to production.
The result of the Nokia proactive method was they got all the first chips made when the fabrication facility returned to production, while Erikson were given their quota only after Nokia. Erikson lost significant market share because of not being able to offer new phones for an extended period, while Nokia had a far shorter delay. The resilience may be in alternatives to moving, or just to source the product, but the most pro-active organization may well gain a competitive advantage.
Resilience is not a once only event. It needs to regularly reconsider the risks in a realistic manner, not just review and acceptance. Risks and their levels will change, and new risks will emerge. To this end, world-class companies also add the practice of posing scenarios to their logistics teams and seeing what risks are identified and what could be impacted. If the previous risk and resilience planning covered these, well and good. If not, the process will have made the teams think through and identify the new risks they might face. Many companies struggled in the global movement of goods when piracy appeared in the Gulf of Aden near the approaches of the Suez Canal. This made many shipments vulnerable and alternative sources or routings had to be considered to minimize the risks until these acts of piracy were reduced in frequency.
We will explore the risks in the next article and then draw all this together in the last article on how to use the risks and their impact to make decisions.
PHOTO CREDIT: Swire Projects.