Scheduling of Project Cargo Moves May Mean Shifting Modes, Sourcing
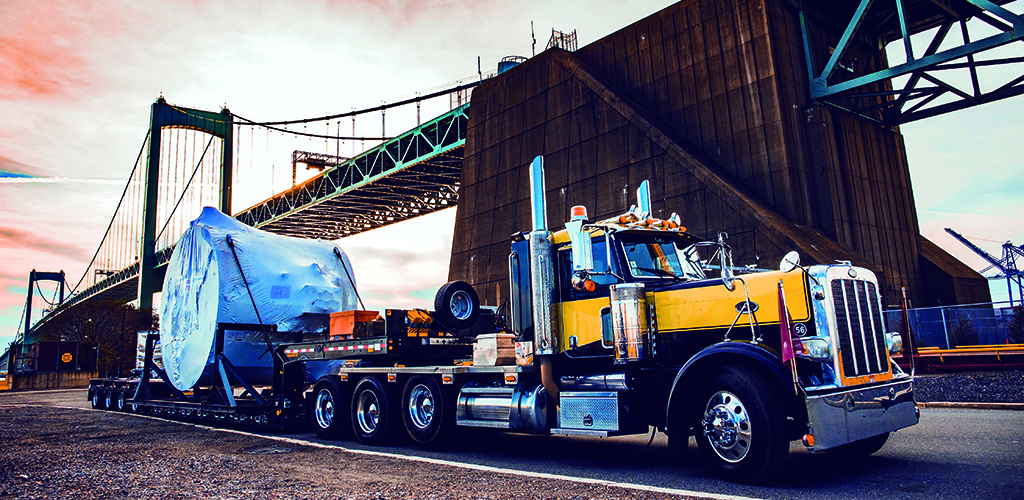
By Paul Scott Abbott
With supply chains challenged by severely constrained trucking capacity, scheduling of efficient inland movement of project cargo may increasingly hinge upon deployment of alternative modes, such as rail and barge, and sometimes broader shifts in sourcing strategies.
“The problems facing project cargo scheduling for inland moves are the same as the problems facing all inland freight moves – historic demand levels for trucking services,” Jeff Tucker, chief executive officer of Tucker Company Worldwide, told Breakbulk.
Robert Sutton, executive vice president of innovation at BNSF Logistics LLC, told Breakbulk that, while a significant number of projects are being put on hold, many of the shipments that are moving may well be better doing so via rail rather than truck.
And a spokesperson for the Port of New Orleans advises that record breakbulk and project cargo volumes transiting the Mississippi River port are more and more relying upon barges for inland transport, thus circumventing long-haul trucking issues.
Demand Tops Supply
With overall demand far exceeding supply of truck capacity, Tucker said his Haddonfield, New Jersey-based third-party logistics firm, which focuses on specialized freight, is looking beyond the bigger motor carriers to secure inland trucking for project cargo.
“As a broker,” Tucker said, “we are able to assemble not just large carrier capacity, but small and medium carrier capacity that the big EPCs [engineering, procurement and construction firms] and BCOs [beneficial cargo owners] really can never get to know on-board. There is only so much any large shipper can do today.”
Citing DAT Freight & Analytics data showing the average ratio of number of loads to number of flatbed trucks to be higher than 18 in nearly all the Lower 48 U.S. states, Tucker commented, “That’s a shortage. Construction, low interest rates, abundant corporate and household cash and the resulting spending, and delayed capital improvement work in big industries like oil, gas and chemicals is keeping the open-deck and project cargo truckers busy,” he said.
“Demand for trucking has been either the highest on record or second-highest on record throughout the past 15 months. We don’t see an obvious end to this, as so many supply chains are still significantly in shift and/or recovery mode.”
As Covid-19 pandemic impacts intensified in 2020, committed volumes for hundreds of thousands of motor carriers and brokers across myriad lanes disappeared, said Tucker, who is a 30-year industry veteran and a past board chairman of the Transportation Intermediaries Association.
“A literal scramble for dear life occurred, with carriers looking for business to replace lost business,” he said. “In the summer of 2020, manufacturers who went dark, or at low production, tried to step up, but ran into supply issues, labor issues and, of course, trucking issues.
“Market participants have spent most of the past 15 months luring capacity away from each other, to serve their own interests,” Tucker continued. “That creates tremendous churn and mind-blowing complexity as we try to understand what the issue is. There is no one issue. There are infinite ripples created by a world’s economy that shut down in 2020 and has yet to fully reopen.
“We are very far away from an equilibrium,” Tucker added, noting that production slowdowns by automakers also are factoring into the equation.
Issues Start at Ports
BNSF Logistics’ Sutton said inland supply chain challenges actually begin at seaports – and sometimes earlier.
For example, he said, the ocean freight cost for shipping a set of wind energy blades to a U.S. West Coast port across the Pacific Ocean has doubled or even tripled, reaching US$120,000 to US$180,000 today, compared with a pre-pandemic price of US$60,000 for a similar shipment.
While such ballooning costs are causing many projects to be put on hold, the project shipments that continue to move forward face issues from the moment they get ashore, if not before, as ships are stuck, for example, for weeks off Southern California awaiting an available berth – and then landed cargo often sits a week or more before pickup by truck. This can create serious challenges in planning for components to arrive on schedule for an installation.
“Once shipments get to ports, there is congestion,” Sutton said. “Projects are facing the same challenges as containers, including labor shortages and tight truck capacity. Just getting the product through the ports has been a challenge. This is especially true as it relates to trucking.”
BNSF Logistics is combating such concerns in multiple ways, including a heightened use of rail for inland moves, as well as greater reliance upon collaboration. In this regard, it shouldn’t go unnoticed that Dallas-based BNSF Logistics is a subsidiary of Fort Worth, Texas-headquartered Burlington Northern Santa Fe LLC, which also is the parent company of Fort Worth-based Class I operator BNSF Railway.
“With the trucking challenges, using rail can help get in front of lead times,” said Sutton, who has more than 25 years of industry experience, including as a BNSF Logistics executive since 2003. “More rail is being used because of the challenges in getting truck capacity.”
BNSF Logistics is leveraging in-transit yards to function as what Sutton termed “shock absorbers,” furnishing a cushion of as many as 90 days for project components, including wind and solar energy units, brought in early and then held for just-in-time delivery to construction sites.
Rail also continues to have advantages related to ability to load components at a seaport such as Corpus Christi or Galveston and move the oversize units by train through a number of states without having to deal with the patchwork of incongruent state regulations for truck transport of such cargo.
‘Collaboration is Key’
Furthermore, BNSF Logistics – which has moved more than 43,000 wind components since 2017 – makes use of innovative technology in efficient rail shipment of such units. One example is a patented saddle fixture for easing the transport of lengthy wind energy blades by minimizing swing and controlling their shape through curves.
Ultimately, according to Sutton, cooperation among shippers and supply chain partners continues to be as crucial as ever.
“On the domestic end, it’s a matter of working closely on the planning side,” he said, observing that, if feasible, it might prove beneficial for product to now be imported from Europe rather than from Asia. “From our end, it’s just a matter of customers working closely with supply chain providers.”
To counter the congestion and bottlenecks, Sutton offered this seemingly universal guidance: “Communication is key. Collaboration is key. Being transparent is key.”
A professional journalist for more than 50 years, U.S.-based Paul Scott Abbott has focused on transportation topics since the late 1980s.
Photo 1: An energy valve is transported by specialized flatbed truck, having found capacity amid a constrained motor carrier market. Credit: Tucker Company Worldwide
Photo 2: Jeff Tucker, Tucker Company Worldwide
Photo 3: Robert Sutton, BNSF Logistics
Photo 4: A saddle fixture, patented by BNSF Logistics, is among innovative solutions deployed to ease inland moves of wind energy components. Credit: BNSF Logistics