Jan 21 | 2022
Seismic Equipment Move Tests Project Detail
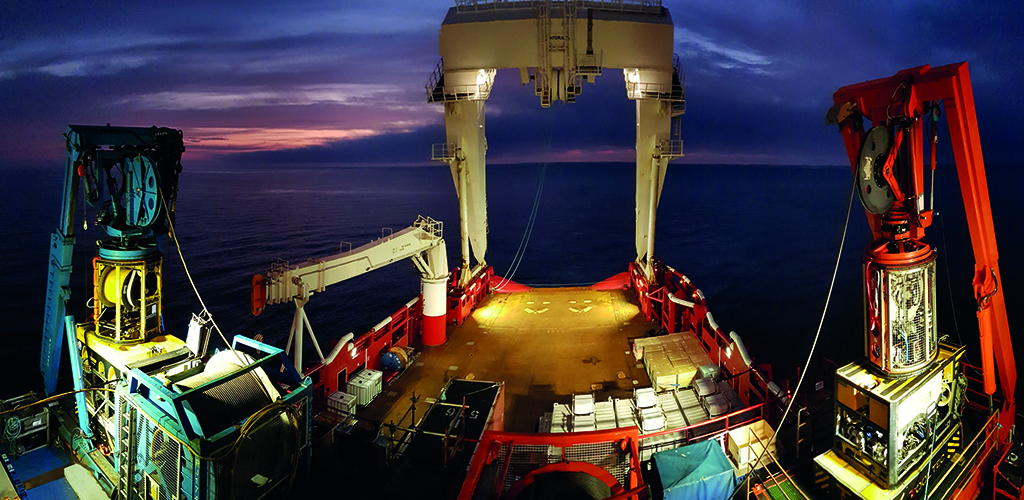
By Malcolm Ramsay
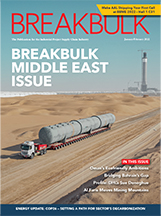
The project, on behalf of Norwegian geophysical services provider Axxis Geo Solutions, or AGS, involved transporting 54 tonnes of seismic gear to the North Sea, for a project that began in June 2021. GAC North America initially delivered the cargo from Houston, and then following the completion of measurements in the North Sea, GAC Aberdeen oversaw return of the equipment later in the second quarter.
“We chose air cargo as this is rental equipment and delivery time was obviously very important,” Andrew Cushnaghan, onshore project manager AGS, told Breakbulk. “GAC presented several solutions, and the whole process, from initial talks to the arrival of the cargo in Houston, was handled for us by GAC key accounts manager, Ajmal Aboobacker.”
Having ruled out sea freight as too slow, AGS chose an airfreight solution via Liège Airport, Belgium, utilizing two flights to keep costs to a minimum, and trucks for transport to and from Aberdeen in the north of Scotland. While reducing overall journey time, Cushnaghan noted that this did add some uncertainty around import and export to the UK.
“We were uncertain, post-Brexit, about sending trucks to Bruges [to meet the cargo flight] due to the potential for customs delays and the consequent financial impact,” Cushnaghan said. “Ajmal was able to assure us of the customs process and helped us prepare the trucks in the best way to facilitate customs handling. This involved separate commercial invoices for each truck – normally we only make one commercial invoice for shipments – and careful loading of the trucks, to match the paperwork.”
Close Communication
Worth several million dollars, the cargo of seismic equipment consisted of multiple nodes containing lithium batteries and required specialist dangerous goods packers and documentation. As a result, close communication between the partners was critical for success. As Jenna Deans, operations coordinator at GAC Aberdeen, explained: “Continual updates on progress, shipping lead times, the loading plan and transport coordinating between ourselves and warehouse operatives was key.”
Having completed the seismic project in the North Sea in the second quarter, AGS then repacked the equipment for shipment back to shore aboard the Assister, a ship under GAC’s agency.
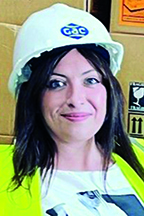
Upon arrival in Aberdeen, the first load of seismic nodes was unloaded and transported to a warehouse owned by terminal operator Sea Cargo, just a short distance away, minimizing cost and time.
“The shipment was split into two lots – one week apart. GAC gave us precise weight and dimension limits for each lot, particularly for each deck of the cargo plane – allowing us to adjust the individual pallet heights to match,” Cushnaghan said. “The clear instructions from GAC allowed us to concentrate on the first shipment – getting the pallets prepared in time for pickup. We were then able to start the second shipment preparation while the first was being picked up. This kept the equipment rental cost to a minimum.”
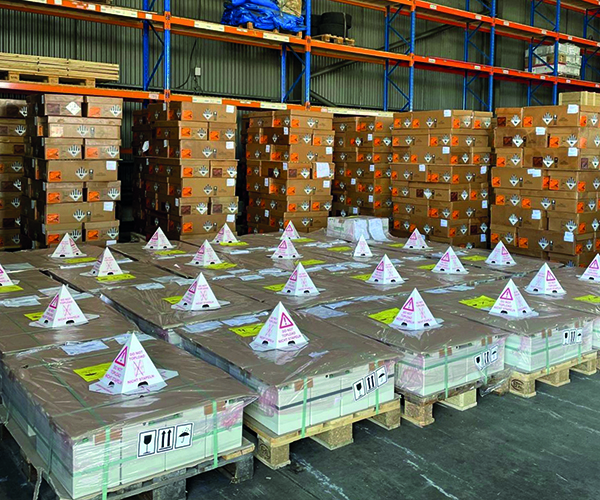
In total, the team from GAC oversaw packing of 165 pallets and as a result of the meticulous pre-planning and coordination, all of these fitted perfectly in the allotted space, meeting weight limits for both trucks and cargo plane.
“This avoided any wasted cost for unused space or further shipments for equipment not able to fit within the limits,” Cushnaghan said.
Accurate Labeling
Once the cargo was safely loaded, the next step was to ensure that all items were correctly labeled and ready for cross-border transit.
Deans noted that the involvement of a third-party dangerous goods specialist was paramount in making the project a success: “We chose to work with Aberdeen Dangerous Goods (ADG) of which we have a great professional relationship, displayed over the years of our collaborating. Their knowledge and expertise in this field is second to none and we welcomed this partnership on the project.”
Working closely with ADG, the team at GAC Aberdeen analyzed the complex UK-to-Belgium clearance procedures and spoke to partners, arranging onward haulage to Liège to ensure that everything went without a hitch. The team then ensured that all documentation was thoroughly checked for accuracy and compliance with regulations, before collating with outbound loading documentation.
As well as collating the relevant customs documentation, GAC also oversaw Covid-19 compliant crew onboarding procedures including provision of a security cabin and officer, the arrangement of lateral flow tests, container hire to move the freight from the vessel to the warehouse, hotel, taxi, car hire bookings and more.
“As we had approximately 40 tonnes of dangerous goods cargo to transship to Houston, the sheer volume and weight of cargo required to move, and ensuring this reached its destination in its protective state as intended, was the only ‘challenge,’ but we were thrilled to excel at this,” Deans said.
Upon arrival in Houston, the cargo was unloaded from the aircraft by local firm Aries Worldwide Logistics for onward transport, with GAC providing the team with all necessary paperwork for efficient clearing and delivery.
“It was a good experience working with GAC on the whole project and Ajmal’s one-point-of-contact for the equipment cargo shipment was appreciated,” Cushnaghan concluded.
Based in the UK, Malcolm Ramsay has a background in business analysis and technology writing, with an emphasis on transportation and ports.
Photo 1: The cargo aboard the Assister, a ship under GAC’s agency. CREDIT: ROBERT COOPER
Photo 2: Jenna Deans, GAC
Photo 3: The cargo was loaded on to pallets specific to the deck heights of the freight plane. CREDIT: ROBERT COOPER