Dec 17 | 2021
Leans on Relationships for Giant Equipment Project
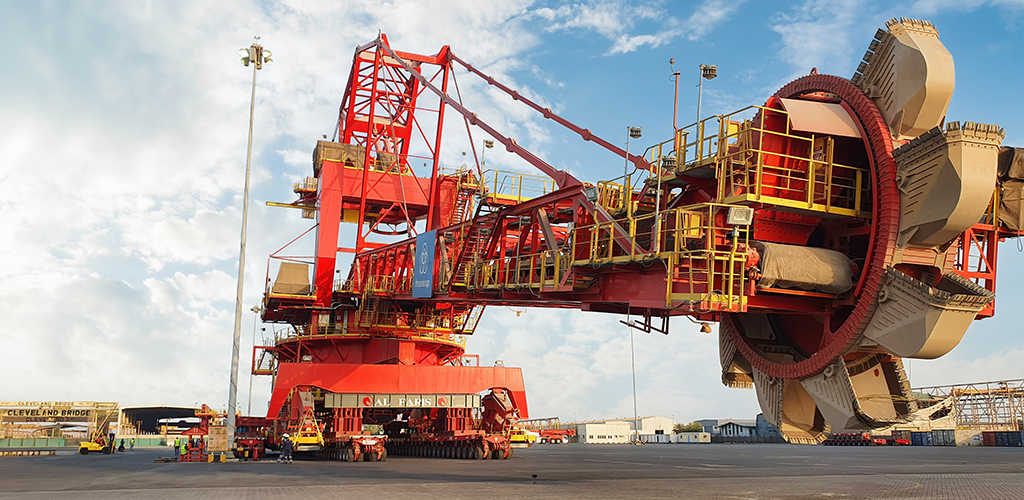
By Malcolm Ramsay
Since the dawn of the industrial age, the mining sector has pushed the boundaries of equipment size and scale as the machinery required has grown in scope. The latest generation of machinery is no different and Emirati breakbulk specialist Al Faris recently experienced this first-hand when it assisted in the transportation, erection and relocation of one of the world’s largest mining machines.
A multi-year project, this transport involved movement of loads of more than 2,000 tonnes each and was completed in partnership with Dubai-based heavy engineering firm Fabtech International Ltd., on behalf of German multinational conglomerate thyssenkrupp Industrial Solutions.
“These are massive structures and the biggest of their kind in the mining world,” Kieve Pinto, executive director of Al Faris Group, told Breakbulk. “Al Faris Group was contracted to transport and assemble components of a shiploader from Fabtech’s nearby fabrication facility. We have been working with Fabtech International for years now and have a great, understanding relationship. Our main goal has always been to work towards the utmost satisfaction of the client.”
Al Faris will be exhibiting at Breakbulk Middle East, Feb. 1-2 at the Dubai World Trade Centre in Dubai.
Unprecedented Scale
As part of this project, the team first had to move several outsized components from the plant to Jebel Ali Port in Dubai. This initial phase took place in 2019, following fabrication work by Fabtech, and involved components for a giant bucket wheel stacker-reclaimer, a tipper car and a linear shiploader. Although Fabtech International’s facility is located less than two kilometers from the dock where the cargo was to be assembled, the sheer size of the machinery meant that this movement was far from straightforward.
Don Moraes, CEO at Fabtech International Ltd., explained that several of the components were moved directly to the dock “in larger dimensions to reduce the delivery lead time,” rather than transporting them as smaller standard components to the construction job site. As a result, the construction of the stacker and shiploader was achieved in record time, with both completed in just nine and a half months.
While this meant that the largest components were moved direct to the port, it still meant that a significant amount of assembly was required once these giant structures reached the dock. Some of the largest components included a huge column structure, which measured more than 62 meters long and weighed 580 tonnes. A platform structure was also moved which weighed 330 tonnes and would form the basis for later assembly of the bucket wheel stacker-reclaimer.
Headquartered in Dubai, Fabtech International is one of the leading steel fabrication firms in the UAE and has experience in developing a range of engineering projects. Alongside heavy fabrication, the firm also specializes in heavy equipment manufacturing solutions for the industrial and marine sector, civil contractors, oil and gas, fuel storage tanks, onshore and offshore facilities, and more.
“Our extensive experience in fabrication of bulk handling equipment meant we were able to offer a range of solutions for this project and ensure that we met the specifications in the most efficient manner possible,” Moraes said.
From Warehouse to Wharf
As a result of the oversized dimensions of these parts, the team planned a careful move by road using multiple self-propelled modular trailers, or SPMTs, along several streets from Fabtech’s facility to the port. To ensure that the structures made it safely to the port, the team from Al Faris carried out comprehensive preplanning simulation to ensure that the swept path could clear all obstacles on route and the cargoes could reach the dock in a timely manner.
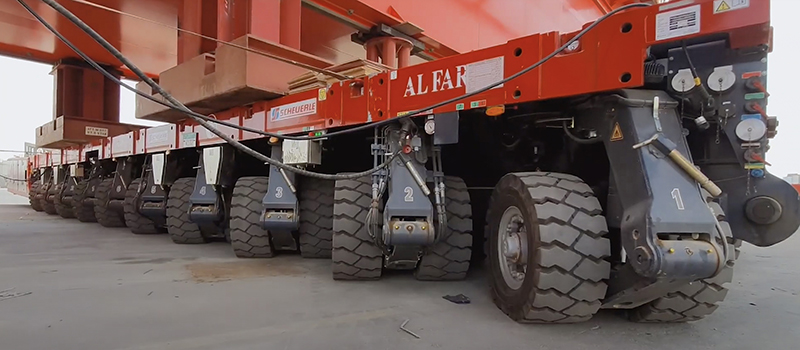
The intervention of the Covid pandemic last year understandably caused some disruption to the plan, and the latest stage of the project saw the partners move the completed structures to a new loading position at the same dock.
“We had completed the loading, transporting and assembling of these mining machines – a bucket wheel stacker reclaimer and a ship loader – at Jebel Ali Port two years ago,” Pinto noted. “After completing some more work from the client, we recently had to relocate the entire loads, without dismantling, to a new position some 150 meters away.”
The breakbulk components, which had seemed large enough when initially moved from the fabrication facility, were now dwarfed by the size of the completed structures. The largest of these was the bucket wheel stacker-reclaimer which measured 98 meters in length, 20.5 meters in width, and 39 meters in height.
This giant structure also weighed 2,100 tonnes, making any movement a major endeavor. Added to this, the completed shiploader measured 128 meters and weighed a further 1,650 tonnes, while the tipper car measured 77 meters in length, and weighed in at 600 tonnes.
“We had to carry out extensive engineering for this move,” Pinto noted, explaining that the teams’ calculations obliged them to construct entirely new load-bearing structures specially for the project.
Close Communications
While the distance was a lot less for this second move, the logistics of the move were many times more complex as the teams had limited margins of error and faced tight deadlines.
“Time was the key challenge. Since the enquiry started, we had only couple of weeks to execute,” Pinto explained.
To meet this tight deadline, the partners drew heavily on the close existing ties between the companies to ensure continual communication between crew and management on all aspects of the move throughout the project timeline.
“We have a 25-year working relationship with Al Faris and this was vital in building the trust and confidence between the organizations and making communication and planning easier,” said Murali Ganesan, Fabtech’s project manager.
Headquartered in Dubai Industrial City, Al Faris has a long history of heavy-lift and breakbulk handling, with more than 25 years of experience operating across the Middle East and North Africa region. Over this time, the company has played a vital role in many of the emirate’s largest construction projects, assisting with development of the Dubai Metro, Dubai Mall, Dubai International Airport, Riyadh Metro, Palm Jumeirah and The Burj Khalifa, among others. The company also offers comprehensive lifting equipment rentals, with one of the largest fleets in the region, comprising cranes, trailers, forklifts, jacking and sliding systems, manlifts, and earth movers.
Covid Restrictions
Along with the time pressure, the crew also faced a challenge in staffing the job at such short notice given the numerous movement restrictions due to Covid-19 and global crew shortages arising from supply chain disruption.
Al Faris’ Pinto noted that a small crew was carefully selected for the job, with Covid safety protocols strictly adhered to from beginning to end, and movement carefully choreographed to limit risks.
“In terms of availability of manpower, logistics and material, the arrival of Covid certainly created downside for preparations and implementation,” Fabtech’s Ganesan explained. “But, in terms of new business and the number of new orders we have seen, I would say there has been a net upside.”
With the crew in place, the partners oversaw the cautious move of the machinery over the 150 meters across the Fabtech Jebel Ali yard to prepare for shipment. In all, 96 axle-lines of SPMT were used, with the team relying on Scheuerle-made fourth-generation trailers.
“This was a milestone project for all three parties,” Ganesan said. “It gained lot of exposure for the mining industry and demonstrated the unique experience and skill we have here in Dubai for handling these sorts of megastructures.
Having reached their new position, the giant machines were then poised for delivery to an iron ore mining project overseas managed by thyssenkrupp in the northwest region of the Gulf. The stacker reclaimer and ship loader each have capacity to handle an estimated 16,000 tonnes per hour.
Commenting on the successful completion of the project, Christian Wohlgemuth, product lifecycle manager for stackers and reclaimers at thyssenkrupp Industrial Solutions, praised the partners on the transport, erection and relocation of the units and the timely delivery of the parts for shipment.
“Our bucket wheel reclaimers are the result of decades of experience and technical competence, and combine robustness with outstanding speed and high throughputs,” Wohlgemuth said, adding that this design includes all the necessary precautionary equipment and systems “to minimize the impact of noise, dust emissions, etc. on operators and the surroundings.”
Headquartered in Essen, Germany, thyssenkrupp is one of the world’s largest steel producers and also manufactures a range of industrial machinery, including mining equipment, high-speed trains, elevators and ships. The group’s subsidiary thyssenkrupp Industrial Solutions is responsible for engineering, construction and maintenance services worldwide and operates more than 17,000 industrial machines and systems globally.
Based in the UK, Malcolm Ramsay has a background in business analysis and technology writing, with an emphasis on transportation and ports.
PHOTOS:
Photo 1: The bucket wheel stacker-reclaimer measured 98 meters in length, 20.5 meters in width, and 39 meters in height. CREDIT: AL FARIS
Photo: Fabtech described this as a milestone project for all three parties. CREDIT: AL FARI