Jun 29 | 2022
Hasenkamp’s Velte Revels in Unique Moves
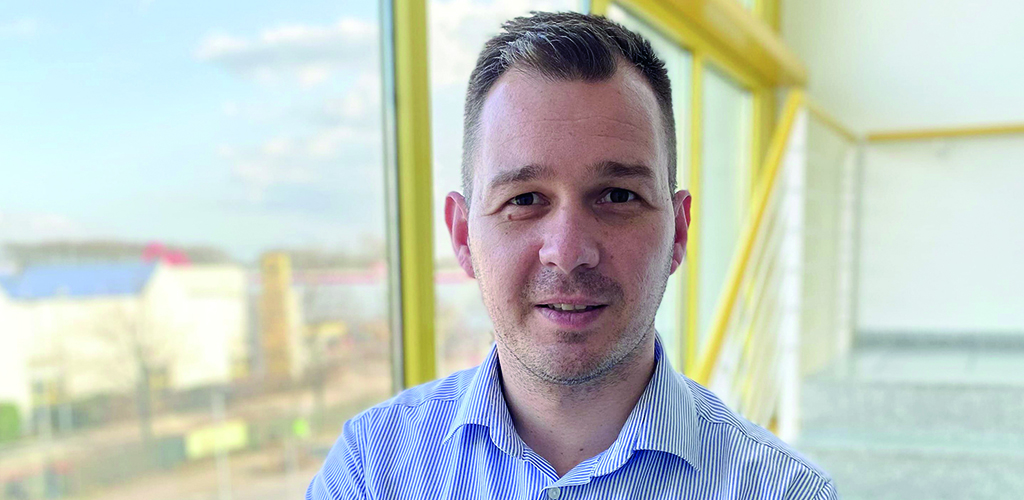
By Felicity Landon
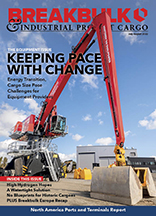
Not so when one is talking about packing, lifting and transporting a pair of 11th century copper cathedral doors, measuring 4.72 meters high and with a width of 1.25 meters (left) and 1.14 meters (right), each door weighing 1.85 tonnes, with little room for maneuver, let alone full-size cranes. And not so when an artist creates such an enormous painting in his studio that it can’t be taken out via the door or window – the only solution being to raise the roof instead.
It would be flippant to describe such challenges as ‘all in a day’s work’ for Stefan Velte, but these are the type of challenges he handles on a regular basis as head of Hasenkamp’s logistics & engineering solutions, or LES, department.
Velte’s department was well known as the ‘art inspection’ unit of the Cologne-based logistics company until the end of last year, so why rename it? Cologne-based Hasenkamp says: “LES sounds international and very technical. And that’s exactly how it should sound. In the many years that the department for special logistics challenges has existed, the demands on the team of 10 have steadily increased. The new English name is intended to reflect this better; and furthermore, it’s used to underline ever-increasing internationalization.”
Velte joined Hasenkamp 15 years ago and joined the department after a three-year traineeship. Since then, he has been involved in moving high-value works of art, including relocations for VIPs with large art collections and valuable furniture, transporting artwork to and from the world’s top auction houses, shipping artwork to and from exhibitions, and supporting museum renovations and relocations. As well as historical artifacts, the team handles highly sensitive and challenging scientific and technical items.
“When we are moving artwork, we don’t have a manual for it – there is no blueprint when you are moving something that has maybe not been moved for 100 years or more,” he said. “We have been a pioneer in this business for 70 years. However, this is not classical engineering.
Transportation Considerations
Manufacturers of huge generators, transformers and other units usually give some thought to how the items are going to be transported to their end destination. An artist who creates a painting measuring 7 by 4 meters and weighing 500 kilograms probably hasn’t. Hasenkamp’s team has moved the entire contents of museums, including artworks and items of stone and wood; that has included de-installing, packing, transporting and reinstalling unique and irreplaceable items that were clearly not created with transport in mind.
“There are nights when I do not sleep very well. When there is expensive art or difficult art to move, then I might lie awake, going through the process step by step, while I have the time to think it through. It is always in your mind – is this the right step? Can we do it another way? What happens if you do this step or that one?”
The most challenging move was that of the Bernward Doors, which were originally made around 1015 for Hildesheim Cathedral in Germany. The largest of their era and each cast in one piece, the doors show relief images from the Bible, and are considered a masterpiece of Ottonian art.
“Those doors were high-tech for their time,” Velte said. “Our challenge was absolutely huge. The doors were being moved because the old church was being renovated; they were moved to another church close by, and afterwards we put the doors back again.”
At the other end of the size scale, the team has moved the Nebra Sky Disk several times. “We always get to accompany it on its travels,” Velte said. “For me, it is as outstandingly valuable as it is beautiful, because with its estimated 3,600 years, it is the oldest testimony to the astronomical knowledge of our ancestors.
“It is a challenge because the glass is very thin and fragile. We have to create a good crate for it while thinking about any vibration or shocks during transport.”
When moving enormous paintings, part of the challenge is the construction behind the wall at the destination site, ensuring this is strong enough to hold the weight.
“Our job is to calculate everything, to plan with our customers, to find the solutions for the museum for them to have their show.”
Away from art, the team also moved the Alpha Magnetic Spectrometer (AMS-02), a €2 billion scientific experiment which was transported across Europe on its way to the International Space Station; Hasenkamp was in charge of planning and implementing the trip to the U.S., to NASA in Florida.
From ‘Nail to Hook’
The team likes to talk about business ‘from nail or hook to nail or hook.’ “We prefer to handle the whole process for transport – planning, dispatch, packaging and installation. There is also Customs to organize, which is very special regarding artworks or cultural goods, and of course insurance.”
Founded in 1903, Hasenkamp remains family owned. It is managed today by fifth-generation owners Hans Ewald Schneider and Thomas Georg Schneider and by Ralf Ritscher.
The company has more than 40 locations worldwide, operations in more than 30 countries and divides its activities into four business units: Fine Art, Relocation, Archive Depot and Final Mile Services.
Increasingly active in the Middle East, supporting the construction of museums and modern art collections in the region, Velte’s team was part of the first move of artwork to the Louvre Abu Dhabi before it opened in 2017.
The ‘small and agile’ core team draws on expert support from the wider company as required, including packers and drivers. “We have art packers who know exactly how to pack the artwork depending on material and climate and temperature conditions,” he said. “We find the right packaging and we have our own carpenters to create our own crates.”
The company operates with partner companies and agents where it does not have its own location. Hasenkamp’s assets range from 600 trucks across the group to intricately developed cranes. These include small cranes designed to lift up to 5 tonnes, to meet the challenges of limited access to museums and other premises. Mobile cranes, forklifts and other equipment are rented in if appropriate. “Sometimes it is better to ship a crane from Germany or wherever – or we can rent on site. It depends on costs and what is required,” Velte said.
Packaging is only one consideration. For artwork and cultural items, storage must be kept at a constant 20-22°C or 68-72°F, the museum standard.
“Our warehouses and trucks always keep to this temperature – no matter what they transport, we always guarantee this,” Velte said.
Hasenkamp has 120,000 square meters of storage worldwide, and this is mainly used for this kind of art and other valuable goods. The temperature and humidity are maintained via a geothermal solution, combined with solar power.
The company was also a trailblazer with the development of crates to maximize sustainability. “Forty years ago, Hasenkamp decided to build crates for art shipments from wood,” Velte said. “We developed a system to enable the re-use of these crates. Some have been in usage for 20 years.”
The company is developing crates made with Kiri wood, which offers a number of advantages, Velte noted – it burns only at over 400°C, it is strong and stable, and it is lightweight, delivering a crate that is only half the weight of a standard unit.
“Light weight is good for us – if we don’t have to transport such heavy things, our carbon is reduced, and we need fewer people to lift it.”
Art Introduction
When Velte joined Hasenkamp, it was his first step from education into the world of work. “I knew nothing about the company; I looked at all sorts of options and when I found Hasenkamp’s home page, I thought it looked interesting and wanted to work there,” he said.
Fifteen years later there have been clear advances. “The technical part is better – cranes are so sensitive. But at the same time, we are seeing more sensitive art, other materials, more fragile items.”
Digital twinning has become an important tool, enabling the team to create computerized simulations. “It is closer to the practice, but it is not the practice,” he noted.
“The real thing is always different. You can’t simulate everything – when you are onsite, everything can change.”
His interest in art has developed too. “When I go to museums, I always look behind the paintings; my question is how did it get in, how was it installed, how everything works. But I also love the art – when you are close to the artist and know the story behind the paintings, that makes it very interesting. I meet a lot of artists – when you can talk with them and they are so close to you, you understand that they want to have the best transport for their artwork.”
Felicity Landon is an award-winning freelance journalist specializing in the ports, shipping, transport and logistics sectors.