May 18 | 2022
Transporters See Disconnect Between Capacity, Affordability
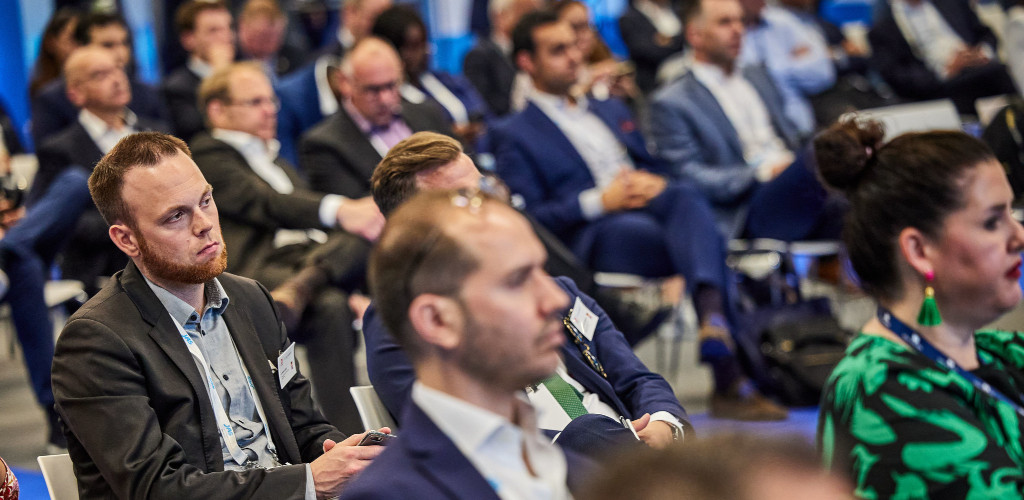
By Mike King
SAME-DAY BREAKBULK EUROPE COVERAGE: Standardisation of wind turbine blade sizes and more collaboration between OEMs and logistics stakeholders will be critical if the current disconnect between transport capacity and affordability, and the shipping needs of manufacturers is to be bridged, delegates at Breakbulk Europe heard Wednesday.
In a session which focused on wind power, delegates heard that war in Ukraine and soaring energy costs were set to drive renewable energy demand for the next decade, with wind power assuming vital importance for many countries.
However, escalating logistics costs and the short shelf life of customised transport solutions are inflating the delivered cost of wind turbines, as well as making it difficult for equipment providers to finance investments.
Antonio Lazaro, director, global outbound logistic & transport solution CoE, LM Wind Power, said wind turbine sizes had increased exponentially in recent years, and this “rat race” among OEMs was now sucking in transport companies “who need to match these investments, even though their investment will be obsolete a few years later”.
He added: “Every seven years our blades grow by 10 metres on average. This means factories need to get bigger, factory equipment needs to get bigger and transportation equipment needs to be changed every 5-6 years. This is an outrageous investment effort that our industry has to make, and the transport industry has to make.”
Thomas Sender Mehl, director, global sales & operations planning and supply chain excellence, KK Wind Solutions, asked how crane providers were affected by the upsizing race in the wind power supply chain. Andreas Ritschel, deputy sales director Mobile harbour cranes, Liebherr-MCCtec Rostock GmbH, said it was not just about the weight that needed to be lifted.
Other factors, he explained, were also the unit’s outreach and, increasingly, whether ports could even safely operate the largest cranes, or use them for other cargoes.
“I remember a time when we thought a crane size of 120 tons or 140 tons would be the biggest crane that would be needed out in the market,” he added. “Then we had the next crane that could lift 200 tons. Then it was 300 tons; then 600 tons. If we now develop cranes for lifting 700 tons or 800 tons, we are not sure customers will even be able to use them for other cargoes.”
Rainer Sasse, CEO, Luxtrailers SARL, said for companies using a transport equipment leasing model, it was untenable to invest in equipment which did not have a long shelf life. “We need to know what’s going to be needed in five or seven or 10 years,” he added.
Morten Nielsen, product functional lead transport, Vestas, said more collaboration was “how we mature this industry”.
Pieter Jacobs, Head of Onshore Wind at Mammoet, also said more collaboration between OEMs and logistics providers on design was required to enable transport providers to more effectively plan ahead. “Innovation costs money,” he added.
He called for more standardisation across the wind turbine sector. “If we can standardise, that leaves more room for innovation to bring the industry together,” he added.
“Financing a standardised transport system is much easier,” agreed Sasse. “The more specialised the system, the more specialised and complicated the financing gets.”
For his part, Lazaro said the wind turbine industry and its transport providers needed to reach agreement on how to move forwards.
The current model, whereby every new OEM design required transport providers to “reinvent the wheel” and invest in a new generation of equipment every few years was simply driving up the landed costs of wind turbines.
“There’s lots of potential in standardising design, and then defining standard transportation systems,” he added.
Check out our post-session interviews with the speakers: