Jun 23 | 2021
Breakbulk to Support Nascent Capture Projects
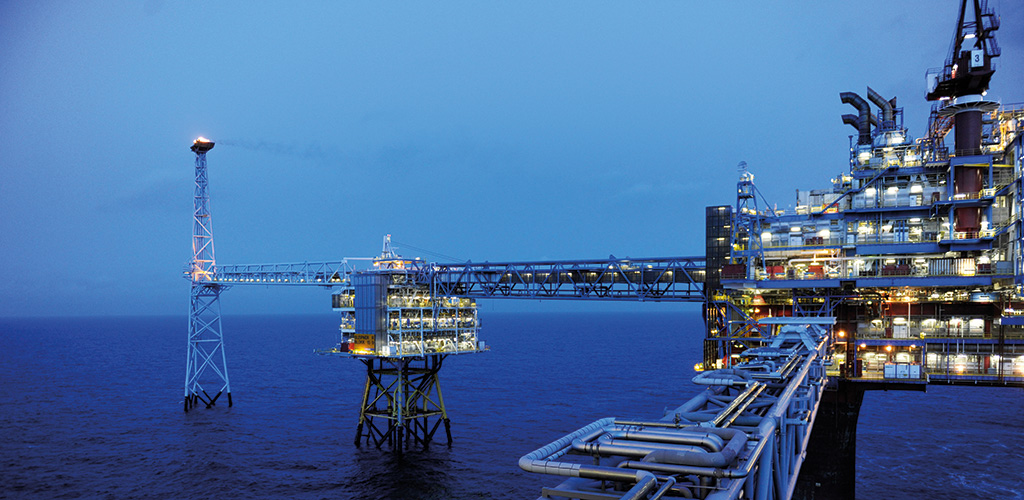
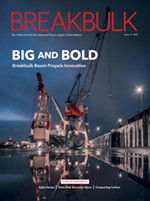
Pipelines, storage tanks, giant compressors, processing equipment, ship-handling facilities – all this and more will be needed for the development and operation of successful carbon capture and storage, or CCS, operations.
It follows, then, that the specialists providing transport/shipping, handling, lifting and installation of such equipment will be in demand.
There is work ahead for project cargo specialists. But, it has to be said, in many cases “ahead” means a little bit beyond the near horizon. While new CCS projects are proliferating and some target start-up dates are relatively close, many projects are still in the study stage. Decisions on logistics requirements won’t be made until the technical and business model details are rather more firmed up.
Driven by pressures and targets to achieve net-zero emissions, global CCS capacity grew 33 percent worldwide last year, according to the Global CCS Institute’s 2020 report. A total of 65 commercial CCS facilities are in various stages of development globally. Twenty-six CCS facilities are in operation, capturing 40 million tonnes of CO2 per year. Many of these are related to CO2 use for enhancing oil recovery, said the institute.
The CCS project in Norway’s Sleipner field, which lays claim to being the world’s first CCS facility, has been injecting 1 million tonnes of CO2 a year for more than a quarter of a century. To give an idea of the magnitude of work ahead, the Global CCS Institute wants to see CCS capacity increase more than a hundredfold by 2050.
CCS technology, and the interest in it, has moved forward rapidly in the past few years, said Chris Gent, policy manager at the Carbon Capture & Storage Association, or CCSA. “A few years ago, CCS was seen at a political level as a helpful tool to achieve climate targets. Now, especially in the UK, Netherlands and Norway, the conversations are about defining the commercial framework for a critical net-zero technology. Once projects have an understanding of the business models, they are ready to deploy at speed and scale,” he said. “A lot of people have been watching CCUS (carbon capture, utilization, and storage) with interest, but now the commitment to net zero and emergence of CCUS clusters has really pressed down the accelerator.
“The implication of net zero means everyone has to decarbonize across the whole economy – and in some areas you have to go further, taking CO2 out of the biosphere. There is also now a lot of public support for net-zero targets and, as the Climate Change Committee has shown, investment in CCUS is one technology to help achieve net-zero. As such, many companies who have few decarbonization options can see that investing in CCUS and aligning with net-zero is a positive thing both commercially and socially.”
In the case of the Sleipner CCS, the driver was Norway’s carbon tax. CO2 is captured from the extracted natural gas, where otherwise it would have been vented to the atmosphere. Once separated, it is now stored safely deep in the rocks beneath the North Sea, Gent said. “This project has been a lynchpin of understanding potential CO2 storage reservoirs, and has been critical for finetuning processes and monitoring and modeling how CO2 behaves in the subsurface.”
Longship Project
A project that is ahead of the pack in Europe is that of Heidelberg Cement in Norway. A full-scale carbon capture and storage facility at the company’s Norcem plant in Brevik, developed as part of the Longship project, was approved by the Norwegian government in December 2020. The first industrial-scale CCS project at a cement production plant in the world, its target is to capture 400,000 tonnes of CO2 a year.
The cement industry is responsible for 6 percent to 8 percent of total CO2 emissions, said Per Brevik, sustainability manager at Heidelberg Cement Northern Europe. “We are a really big emitter. However, to defend ourselves, part of these emissions are unavoidable because two-thirds are from the chemical process – therefore, carbon capture is an interesting measure.”
The plant is on the western side of the Oslo Fjord, 170 kilometers south of the capital. Work on this project started 10 years ago. “We started with desk studies and have taken it step by step, with feasibility study, concept study and then engineering and designs,” Brevik said. “After approval by parliament in December, our part of the project started in January.”
The first stage is demolition of old parts of the cement plant and moving other parts, to create the space to build a plant to enable capture, conditioning and intermediate storage of CO2.
“However, we are also producing cement at 100 percent of capacity, and that will be a key issue – production at the same time as building the new plant. This will definitely require a lot of scheduling and planning.”
The schedule will make maximum use of the plant’s annual three- to four-week winter repair shutdown. The clearance work will take place in 2021 and 2022. The capture plant itself is due to arrive early in 2023 and construction will move ahead. Commissioning is due to start in the second quarter of 2024, ready for the arrival of the first shipment with captured CO2 in June/July.
“This is a huge building project. To some degree the equipment will come by barge in modules, although most will be built at the plant,” Brevik said. “The machines and compressor will come in as units to be connected to the rest.”
Carbon capture technology has to some degree developed in parallel with the offshore industries, he said. “Many of the companies we are involved in have experience in the offshore industry, and of course there you have a lot of good expertise with scheduling and so on.”
The project manager is a Norcem employee, and others will be involved in the project full time. However, much of the management is being outsourced, and Norcem is working closely with the main technology provider, Aker Carbon Capture, the supplier of the capture plant, and the Danish equipment supplier FL Smidth, responsible for integration between the capture plant and the cement plant.
About 1 kilometer of pipeline will be laid, linking the capture plant, intermediate storage and loading station. Norcem will be responsible for operations up to the point when the CO2 is in the tanks on the ships.
At that point, the responsibility shifts to the second partner in the Longship project. Northern Lights, whose partners include Equinor, Shell and Total, will build an open-access CO2 transport and storage infrastructure and transport the CO2 by tanker to a purpose-built receiving terminal. The facility will provide capacity above and beyond what is required by the Norcem site. Heidelberg Cement has eight CCS projects at different development points, with Brevik being the first.
UK Cluster Projects
In November 2020, the UK government announced £1 billion of funding to support the development of four CCUS cluster projects by the end of the decade. The ambition is to have two clusters operational by the mid-2020s and two more by 2030, CCSA’s Gent said. Funding and government strategy is crucial, he added.
CCS discussion in the past often struggled with the “chicken-and-egg” scenario. “Build the CO2 storage infrastructure without a guarantee of CO2 supply? Or capture the CO2 without a developed store to put it? This is why government support to help develop the whole value chain together in CCUS clusters is absolutely critical.”
Meanwhile, he said: “Something that is not perhaps deeply considered outside of the CCUS sector at the moment is how some of the port facilities involved are going to be able to accommodate building of the infrastructure while ships continue to use the port, especially as the UK looks to scale up offshore wind. There is an emerging discussion about coordination between users of the offshore and port facilities to ensure offshore energy projects can develop safely and don’t unintentionally prevent each other progressing. Net-zero will certainly involve a concerted logistics coordination effort.”
The CCSA is facilitating a supply chain group that is looking at the market and the potential UK opportunities ahead. “Within this, we have had a look at modularization. At a high level to what extent could you modularize or standardize components, and what does that mean in practice?” Larger projects often need bespoke solutions and the scale for some of these larger projects is substantial, involving construction of amine scrubbing towers of 50 to 60 meters high, the installation of large pipeline networks and the shipping of large gas compressors. Other projects may be suitable for a more modular approach, perhaps using road or rail solutions.
Scaling Up
In Sweden, the CinfraCap project aims to create joint infrastructure for the transport of liquefied CO2 extracted using CCS technology. The project’s partners, Göteborg Energi, Nordion Energi, Preem, St1, Renova, and Gothenburg Port Authority, are seeking the most effective way of approaching the industrial scale logistics system required to support CCS. The aim is to link it into other CCS projects and to create an open access system so that third parties can connect in the future.
A pre-study published in April 2021 noted that the volumes captured will increase in stages, with the plan being to expand the facility in modules as required. The number of vessels and ship calls would also increase gradually.
The intention is to start capturing CO2 in 2025, said Karin Lundqvist, business development manager at Preem. Discussions continue, including around the business model and permitting and construction issues.
“Regarding logistics [for the construction/installation], I would expect we will have physical construction and equipment one or two years before start-up. We are much too early in this project to start to look at logistics questions – we haven’t even decided who would do the design. Of course, there will be pipelines, storage tanks and other large equipment.”
The plan is to start small and then scale up, mindful that not all industries capturing CO2 will start at the same time. “Some will start in 2025, then it will be a gradual build-up to 2030. So we are thinking of building in a modular way to build up capacity,” Lundqvist said.
CinfraCap is not far behind Norway’s Longship project, aiming for opening in 2025 against Longship’s 2024 date.
There are third parties interested in connecting to CinfraCap, and Lundqvist recognized that it would be a waste if all companies try to build up storage capacity and pipelines on their own. But while CinfraCap has found a technical solution, there are still a lot of hurdles to overcome, including business models, who would own the infrastructure, permits, and so on. “It is usually said about CCS, it is not the technology that is the hardest bit – it is the rest.” Every part in the chain has to be ready at the same time, from actual capture through transport to the harbor and the storage facility, and that will inevitably include movers of breakbulk cargoes supporting global CCS ambitions.
Felicity Landon is an award-winning freelance journalist specializing in the ports, shipping, transport and logistics sectors.
Image credit: Kjetil Alsvik, Equinor Statoil