Heavy-lift Equipment Stepping Up to Climate Challenge
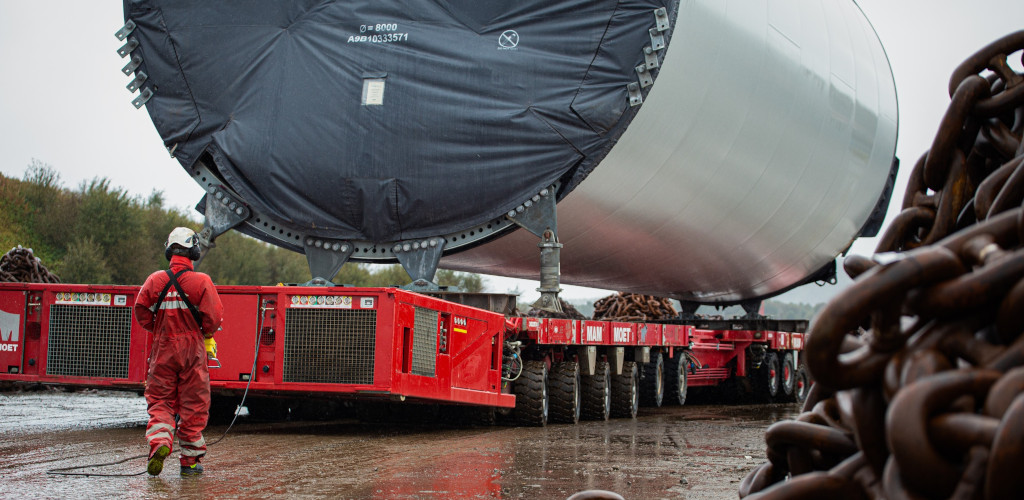
From Issue 6 of Breakbulk Magazine, we speak to industry heavyweights Mammoet, Liebherr and Konecranes to find out how heavy-lift machinery manufacturers are coming up with a range of options to improve the carbon footprint of SPMTs, cranes and other material handlers.
This year, Mammoet announced it was offering a zero-emission option for self-propelled modular transporters, compatible with any trailer in its fleet. The retrofit system “represents another step towards zero emission on site, eliminating the carbon footprint of SPMT transport entirely,” said the company, which developed the SPMT nearly 40 years ago.
“The SPMT revolutionized heavy industry by maneuvering practically any load safely, efficiently and with precision. This next step in its story will be just as significant, reducing their CO2 and NOX emissions to nil and pointing the way towards a sustainable future for heavy transport,” said the announcement.
Mathias Hoogstra, head of sustainability at Mammoet, told Breakbulk that many customers are looking to reduce the carbon impact of their operations, from the largest projects to the smallest.
“Hywind Tampen floating wind farm, with which Mammoet was recently involved, is offsetting 200,000 tonnes of CO2 emissions from industry in the North Sea. Also, many organizations in the civil sector are moving towards a zero-emissions onsite environment. Demand for lower carbon lifting and transport solutions is steadily growing, and our investment in technologies such as the electric SPMT, electric skidding systems, the SK series of cranes, and so on, means we are well placed to help our customers to meet these demands.”
Mammoet said it is the only engineered heavy lifting and transport company with a dedicated innovations and R&D department separate to operational activity.
“So naturally, we are always working on ways to bring additional value for our customers, whether that is lifting heavier, transporting faster or – in this case – working less carbon intensively,” Hoogstra said. “Having said this, we are proud to work with partners across heavy industry and in government to find a path to sustainability for large projects, as was the case here.”
Mammoet has 5,361 axle lines of SPMT, with a total capacity of more than 230,000 tonnes. At present, it has capacity for a few dozen axle lines of electric SPMT, but Hoogstra emphasized that the solution has been built to be deployable at scale, and conversion is taking place in line with customer demand. “We expect this to be highest in Europe in the first instance, as stringent environmental legislation in the country means that many of our customers are looking to decarbonize their supply chain. We are proud to be at the forefront of this.”
Mammoet said the power pack units, or PPUs, vastly reduce noise levels at project sites; in locations where sound restrictions are in place, longer operational windows are now possible. The conversion process involves replacing the diesel powertrain by installing SPMT PPUs. Once retrofitted, each trailer combination has comparable power to existing industry standard units.
“The powerpack development requires investment – however, the value it delivers is significant,” Hoogstra said. “It helps to extend the lifecycle of equipment, which is advantageous from a sustainability perspective. As well as helping customers to decarbonize their own operations, it brings down maintenance and fuel costs relative to an internal combustion engine (ICE) solution. With tens of thousands of SPMT lines globally, this is also a significant step towards making heavy industry sustainable over the long term.”
Mammoet’s SK series of cranes can be fully electrically operated, he added, and the company is working on retrofitting other equipment to operate from battery or mains electric power. “We are also actively purchasing world-first electric equipment from our existing suppliers.”
Battery Drive Options
Konecranes has offered electric-driven Konecranes Gottwald mobile harbor cranes, or MHC, for many decades and every Konecranes Gottwald MHC is retrofittable with external power supply, Robert Vennemann, MHC marketing manager, told Breakbulk.
“When terminals have harbor mains, we offer these cranes with external power supply for many voltage areas. Since the market launch of the most recent Generation 6 in June 2021, Konecranes now provides a battery drive for all its models. These battery systems offer sufficient power for traveling the crane and some cargo movements when the crane is unplugged.”
Konecranes helps customers to reach their climate targets by offering equipment with low-carbon power options and energy-saving solutions, said Sustainability Manager Laura Sarkkinen. “For example, regenerative braking and electric alternatives for terminal operations can reduce the product lifecycle emissions during its use phase by 60-80 percent, according to Life Cycle Analysis calculations verified a third party.”
However, Sara Malagoli, marketing specialist for lift trucks at Konecranes, noted an important point: “When talking about zero emissions equipment, let’s be clear – there is no such thing as a zero-emission vehicle. Steel body panels don’t grow on trees. Lithium doesn’t flow out of the ground and into battery plants. Electricity – even if it’s generated by solar panels – isn’t captured without a great deal of capital and carbon expense. There is too much focus on ‘tank-to-wheel’ while it should be from ‘well-to-wheel’ emissions."
CO2 emissions from machines, or tail-pipe emissions, are nil for battery electric vehicles (BEV), and up to 2.6 kilogram per liter of diesel for ICE, Malagoli said. “Considering also CO2 emissions from the generation of electric energy for charging the BEV batteries, the total ‘well-to-wheel’ emissions vary from essentially zero (renewable electric energy) to even worse than ICE (electricity generation from coal power). However, in most cases ‘well-to-wheel’ CO2 emission is significantly lower for BEV than for ICE.”
Konecranes has chosen a state-of-the-art, responsibly sourced lithium-ion NMC battery-electric solution with the greenest cells in the industry, 95 percent recycled for its E-VER electric forklifts, Malagoli said.
“When it comes to lift truck products, we offer various Ecolifting solutions such as Power Drive and Flow Drive to reduce fuel consumption, carbon emissions and costs while keeping the same equipment performance.”
Array of Choice
Breakbulk equipment manufacturers hear customers asking for a variety of potential solutions today: everything from 100 percent battery electric vehicles through to hybrid drives, CNG ICE and even hydrogen ICE powered machines.
“Today it feels like there is a vast array of potential technological solutions being developed and no one knows which will be the dominant solutions for the future,” said Jeffrey Stokes, Konecranes director product and technology management, Lift Trucks.
“Often we see customers have clear ambitions or commitments when it comes to sustainability and carbon emissions reductions, and they approach us to support them in this. However, they often have a slightly different opinion of how this should be best done. Often key aspects like their operational function, geographical location or local natural resource availability will sway them to a certain type of technology solution and they come to us asking us to support that.”
There is pressure out there, Stokes added: “Some of it from clients, some from company boards of directors, or local regulatory bodies – some even from a self ‘do right’ principle. There seems to be no single common drive – it can be quite local and individual.”
Creative and positive regulation changes, or carbon taxes, could drive change faster but there needs to be a practical approach as well, he noted; it is pointless to push for full electrification unless you have plans for the infrastructure to charge the equipment with.
Funding will continue to go a long way to help innovation, he said, “but the crux comes when the funding stops and the hard reality of technology readiness and commercial viability become key. This we have seen in our industry over the past decade and in other adjacent industries, and I am sure will continue to be the case for whatever the future brings.”
In practical terms, the main challenge for MHCs is the high power demand of cranes handling heavy cargo or providing high handling rates, Vennemann said.
“Using harbor mains has been the easiest way for decades but batteries don’t deliver enough power density for such unplugged applications at the moment. But this is maybe just a matter of time in the overall development process.”
All-Electric Portfolio
Liebherr said that besides its well-established hybrid options, it continues to expand its portfolio of all-electric options. One of Liebherr’s latest developments in the heavy-lift ship crane sector is the all-electric LS 800 E, which offers lifting capacity up to 800 tonnes and tandem lifts up to 1,600 tonnes.
Meanwhile, the LHM 800 MHC, described as the most powerful mobile harbor crane in the world with lift capacity up to 308 tonnes and tandem lifts up to 616 tonnes, is available with electric drive and systems such as Pactronic, Liebherr’s hybrid drive system; this features an additional energy storage device, or accumulator, which is charged when the load is lowered or if there is surplus power from the conventional drive unit.
Liebherr describes the Pactronic system as an impressive power booster which speeds up lifting and lowering times without changing the primary power and reduces fuel consumption.
“For more than a quarter century, Liebherr mobile harbor cranes do not emit any CO2 during operation when our electric drives are in operation, according to Scope 1 GHG protocol, and provided that the customer has the corresponding infrastructure,” said Mathias Haugner, marketing manager – maritime cranes at Liebherr-MCCtec Rostock.
“The expansion of the infrastructure is therefore the key to sustainable operation of the port equipment. In the MHC sector, we are focusing significantly on electrification (E-Drive), HVO and efficiency improvements such as Eco-Mode and Pactronic, which will continue in the future.”
Liebherr’s focus is not only on new equipment – younger diesel-powered equipment in the field can be converted. “In addition, one of our standout programs is Liebherr Reman. It is not strictly related to retrofitting diesel engines for electric power, but up to 75 percent of raw materials and energy can be saved through the remanufacturing of used components and the CO2 footprint is reduced by over 50 percent.”
An increasing number of customers are demanding electric drives in the MHCs they purchase, Haugner said. “There are also customers who require proof of sustainability in the manufacture and operation of our mobile harbor cranes. We are able to provide this evidence. One example is a gold award in the EcoVadis rating.”
With customers creating sustainability or zero-emission strategies for the midterm future, as a supplier, Liebherr demonstrates the possibilities and vision for a “hand-in-hand alignment” he added. Liebherr’s pre-development and innovation management team looks at the megatrends and one example of its focus on new technical solutions and gathering of knowledge is the group’s battery competence center.
“We’ve seen an increase of as much as 280 percent between 2019-2022 of cranes with electric drives. Hybrid drives have also been offered for over two decades, demonstrating that there has generally been a demand for providing electrification in operations by our customers,” Haugner said.
Mammoet and Liebherr Maritime Cranes will be exhibiting at Breakbulk Middle East 2024, taking place on February 12-13 at the Dubai World Trade Center in the UAE.
TOP PHOTO: SPMTs are the workhorse of heavy industry. CREDIT: Mammoet
SECOND PHOTO: LHM 420 mobile harbor crane from Liebherr runs on HVO100 diesel CREDIT: Liebherr