Apr 06 | 2023
AAL, NMT and thyssenkrupp Join Forces for Australia Reclaimer Move

By Thomas Timlen
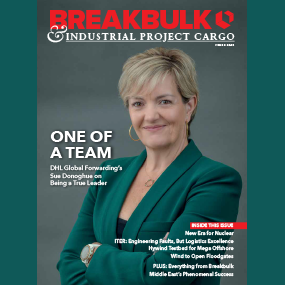
The seven fabricated breakbulk iron ore reclaimer components needed to move from the place of fabrication near Henderson, Western Australia, to a mining facility in Nelson Point.
The cargo included a 95-tonne pantograph, a 278-tonne bucketwheel boom, a 37-tonne reeler platform, a 284-tonne slew deck, a 226-tonne substructure and two 133-tonne 32-wheel equalizers, together adding up to a total volume of 15,790.14 cubic meters.
These components made up the ocean leg of the operation; an additional five modules were transported by road, some measuring up to 8.5 meters in width. A further 38 general and out-of-gauge trailers of ancillary goods were also moved from Perth to Nelson Point to complete the shipment.
For an operation of this scale, industrial engineering giant thyssenkrupp Industrial Solutions turned to the expertise of NMT Global Project Logistics who in turn recruited trusted service provider AAL Shipping and its scheduled monthly Asia to Australia West Coast Liner Service.
The collaboration was not limited to the logistics of the move, but also gathered the partners’ experts to address the engineering and design contributions for the refurbishment of the reclaimer that had been in storage for ten years.
NMT Global Project Logistics senior project manager Jayme Bailey told Breakbulk that he was most impressed by the flexibility of the engineering team in pursuing workable solutions.
“This machine was built 10 years earlier and left in storage. The principal client requested the unit to be refurbished to increase its overall capacity and as such the engineering and design input came from all parties – thyssenkrupp, NMT and AAL – to make sure that the rebuild of the machine factored in all aspects of not only the build, but also the transport and logistics.
“This meant many lengthy meetings were had with the AAL engineering team, NMT, the principal client and the fabricator. The ability to adapt and change, to come to a solution that worked for all parties was a paramount focus and the AAL engineering team rose to the challenge. One of the major reasons for success on this project is attributed to having this input and the fluidity from the AAL engineering team.”
Bailey described the project’s challenges: “From an operational sense, this project was on an extremely tight deadline with some heavy penalties for late delivery of the goods to site. As this project was on the critical pathway for a debottlenecking project and was to be delivered during a peak shutdown period, the window for transport and logistics was extremely rigid. The AAL team managed to keep their liner vessel on schedule during one of the worst periods of port congestion that has been seen over the past five years. This was no easy feat and the outcome of being able to achieve this was a resounding success as the goods were delivered on schedule without any delays.”
BRINGING TRANSPORT STRANDS TOGETHER
Careful planning was required to coordinate the movements by land, then sea, then by land to the destination. Dividing the project into a number of different logistics silos ensured that the appropriate expertise was applied to each stage, beginning with the movement of the goods from the fabricator’s location to the Australian Marine Complex Henderson port facility.
“Due to the size of these units, the goods were transported to the port over a full road closure on self-propelled modular transporters,” Bailey said.
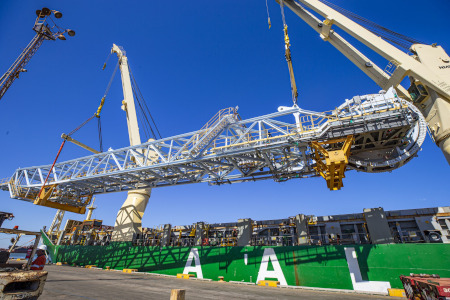
Once at the load port, SPMTs were again utilized rather than conventional trailers. The loading plan was implemented with the super modules delivered alongside the vessel for loading as needed. The entire loading operation was conducted over four-day shifts.
Here the modules were prepared for loading on board the 18,697 deadweight-tonne general cargo ship AAL Nanjing. Extensive planning ensured that this loading operation went smoothly. AAL’s head of transport engineering, Nicola Pacifico, said: “Due to the large and unconventional size of the reclaimer components, which covered a total area on the vessel of more than 1,800 square meters, the lifting and stowage challenges were significant.”
The detailed engineering process started mid-February and ran until the third week of September, one week before shipment – in total, just over seven months.
OPTIMIZING THE DESIGN
Pacifico said that from the preliminary drawings through to the final issue for construction, several steps needed to be evaluated jointly with the thyssenkrupp engineers to ensure a smooth and safe operation from A to Z. “The biggest engineering challenge of the project was the particular design of the reclaimer units and having all the components ready in place in order to optimize the final installation on site and minimize any possible downtime or unforeseen extra costs.”
The reclaimer units were fabricated with several protrusions and a steel construction that required a specific lifting arrangement/geometry for each component and temporary transportation supports that could be removed with minimal manpower and external assistance of lifting and handling machinery.
The decision was made to use bolted steel columns or support stands in combination with additional hardwood for stabilizing and to load spread the weight of the units on vessel decks. “To give a rough idea, some of the supports used due to the bottom structure and protrusions exceeded three meters in height,” Pacifico said. Road transportation requirements also played a big part in the final design consideration, he added.
To cope with the design challenges, the solution for the sea fastening was a combination of H beams and steel stopper plates against the units, plus lashings from the components themselves, to counteract the accelerations during the voyage, especially the uplift forces.
The engineers also had to take account of sea state in the region. “In terms of the sea and weather conditions, we had to consider that in Henderson the allocated berth AMC 4 is nominally swell affected and an easy roll of about 10s period +/- 0.2 degrees,” Pacifico said. “This was evident throughout loading, but due to the motion analysis verification we knew that the swell and roll would not delay or affect the planned operation.”
Once the AAL Nanjing reached Port Hedland, operations began to complete the move to Nelson Point. “This was a reverse operation as noted in the loading, with SPMTs conducting the movement of the goods from the ship’s side to a temporary backstack, staged while waiting delivery out,” Bailey said.
During the loading and discharging operations, AAL’s appointed port captains were described as “absolutely vital” to the successful operation of this project by Bailey. “Their ability to mitigate risk, work towards the best outcome, and roll with the punches had a major positive impact on the project.”
NMT then began the final part of the operation: moving the cargo to Nelson Point. “The super modules were transported on the full road closure over two nightshifts so as to limit the impact to the general public,” Bailey said. “The transport of eight kilometres from the port backstack to site took over eight hours on SPMTs.”
Once at the site gates, the goods were delivered into the nominated site laydown. A large amount of planning went into the site movement to make sure there was clear access to the site and rail approval, as the goods traversed active rails to reach the nominated unloading area.
REAPING BENEFITS OF PLANNING TIME
The time allocated for the careful planning paid off. “Our collaborative, team-oriented and hands-on approach proved a winning recipe for all stakeholders on this important project. Buy-in from our trusted service providers and a shared willingness to go the extra mile ensured the project was executed without issue, on-time and more importantly, on budget,” Bailey said.
AAL Australia’s general manager Frank Mueller agreed: “We are delighted to continue our strong track record for NMT and thyssenkrupp Industrial Solutions, both of whom we are proud to have worked with in the past on domestic industrial projects across Australia.
“The local multipurpose shipping market is still challenging since Covid-19,” Mueller continued, “with port disruptions and labour issues affecting schedules and normal operations. The Australian project sector itself has also experienced upheaval and will continue to weather difficult external conditions until a possible peak of investment of A$95 billion per annum in planned infrastructure between 2023-24 and 2025-26.
“We will therefore continue to ensure our services within the sector remain consistent and keep delivering for our customers despite any and all market challenges.”
Thomas Timlen is a Singapore-based analyst, researcher, writer and spokesperson with 31 years of experience addressing the regulatory and operational issues that impact all sectors of the maritime industry.
MAIN PHOTO: AAL discharging stacker reclaimer at Port Hedland. CREDIT: AAL