Correct Documentation, Funds Movement Expedites Delivery
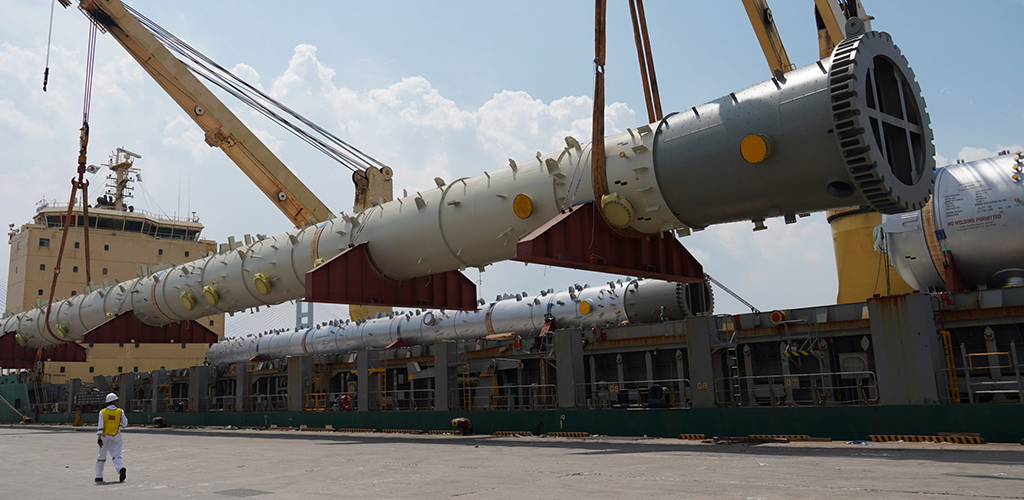
In another installment of a series by former Halliburton Vice President of Global Logistics John Vogt, you’ll gain the critical information needed to reduce shipping risks to your company whether you’re the buyer or shipper. Look for John to continue to provide industry insights in the coming months.
Before we move to other trade issues, lets round off the Incoterms® themselves with a study of a situation so we can look at the principles and provide a more practical viewpoint.
The use of Incoterms® is one part of the trade contract where logistics personnel should be involved, as it defines the scope of the work they must perform. They need to ensure the Incoterms® rule and the other aspects such as named place, loaded or unloaded, special insurance and routes are precisely covered. Logistics is complicated enough with more than 25 entities involved in an international movement, that imprecise agreements lead to significantly higher risks, and ultimately costs. And practically, even if they did not have a hand in the definition of the trade, they will be blamed if the movement incurs problems!
Illustrative Example
To illustrate this, let’s look at a breakbulk movement. Your company arranges with a supplier in Asia to purchase a large, expensive item which must be delivered to your facility in Colorado. In discussions, the seller agrees that they will deliver to the Port of Los Angeles, where your company will unload the ship and move it to your facility. The item weighs more than 50 tonnes and measures 50 meters long, so it will be moved on a breakbulk ship. No discussion on maritime insurance takes place. You query this and the person who negotiated the purchase leaves this to your judgement and asks you as the logistics person to decide on the Incoterms® rule and “whatever is needed.” The item took nearly 18 months to manufacture and is an essential, unique piece of equipment.
This seems somewhat simple to the buyer and seller, but to the logistics side of the business this is neither precise nor simple. The obvious choice is to use a C term, as this matches the sellers responsibility. You’ll also want to protect your company, so you want to ensure the quality of offload, transport and delivery, which is your responsibility. As this is a delivery of a large, expensive item to a port of discharge, you’ll want to use CIF or CIP. The use of CIF would include maritime insurance at class C, the somewhat lesser insurance level.
Of course, this insurance only covers the maritime movement under CIF. It doesn’t cover problems if the item is damaged or lost to your company, which would be looking at an 18-month delay in its project to replace it. For these reasons you’ll choose CIP with the more comprehensive insurance of Class A, and realize you must specify the point of manufacture in the agreements so the whole move is covered to the port of discharge.
You decide on a Terminal X as the offloading experts, and transport company Y to collect and deliver the goods. The contracts with these companies must include insurance that if the item is damaged and the project delayed, they will compensate your company. While they can carry their own insurance for their portions, it is worthwhile to talk to the insurance company covering your company and get a policy for this item which covers the delivery from manufacturer to your plant and its installation process. This might well be far more cost effective than the individual companies involved seeking policies for small portions of the movement. On top of this, you ascertain from the project scheduler that the item is needed on site on Date Z. It takes 2 weeks to unload and move from the port to the site.
Advising the Purchaser
Your advice to the purchaser is to incorporate the following:
Institute an inspection by a reputable agency of the item before it is loaded onto the ship and after loading.
Incoterms® rule chosen:
1. CIP (Terminal X, Port of Los Angeles, USA) Incoterms® Rules 2020.
2. Manufacturing point is Place R.
3. Delivery to be effected prior to Date Z by 2 weeks.
4. Insurance to be Class A from Place R to Port of Unloading at Terminal X (see insurance options below).
5. Documents to be provided within 24 hours of loading:
- Bill of Lading from shipping line (add to their agreement).
- Certificate of origin.
- Hazardous Certificates if any.
- Inspection Certificates.
- Licenses if the goods so require.
- Commercial Invoice for export and import.
Insurance policy comparison between policies from movement organizations against your company taking one policy:
• From date of leaving the manufacturing facility to date of installation on site by your company, OR –
• Class A by supplier from manufacturing point to discharge port, plus your company covering unloading and transport to the end destination, or –
• Class A by supplier from manufacturing point to the discharge port, plus individual equivalent insurance contracts from the unloading terminal and from the transport company.
Contracts with Terminal X and Transport Y with requirements for specific damage payments:
• Handling agreements and methods to be written into a scope of work.
• Delivery documentation for each stage of the movement agreed so specified inspections occur on ship, offloaded at terminal, on the transport and on delivery to the end destination.
• Specification of times for Terminal to unload vessel, and to load Transport.
• Communication from Terminal to Transport so the item is loaded directly onto Transport on the quay, not stored and then reloaded onto the Transport
• Communicate immediately when the ship is available for unloading, is unloaded, loaded and secured on the Transport, arrival of the Transport on site and unloaded.
While there may be more to this in some cases, this shows the scope of a logistics professional’s attention to detail and precision. It minimizes the potential for issues by minimizing the handling in the Terminal and allows for specific actions with inspections along the way. It will allow for a clearer definition if there is damage as to the cause and responsible party.
Broader Logistics Role
It becomes apparent that the work of the logistics specialist is far wider than the mere choice of an Incoterms® rule! This deals with the physical movement; but as we know, as professional logistics experts, there is also the information and funds flow to consider.
Our first action is to choose the customs broker and the documentation they require. It is amazing to many professionals how few people understand that the information flow either enables or delays a shipment and, as such, the documentation delivery and quality is of equal importance to the actual movement of the goods. In the case of the customs broker, the payment of the duties is equally important as most countries will not allow the goods into commercial circulation until the duties are paid.
In the next article we will look at the detail of these documents and what constitutes correct documentation, and then add some issues that many companies include which makes their documents convoluted. For this article, the flow of documentation is important, as this is what will make the goods move towards final use.
Electronic Filing
Many parties involved in trade do not realize it, but with the advent of electronic filing, it becomes feasible to submit the customs declaration prior to the goods arriving in the country. With most of the customs authorities basing their inspection choice on the risk profile of the shipper, the goods, and the country from which they are coming, this allows the computer systems to show the clearance for the container or item well before it is unloaded in the country of destination. This allows customs duties to be paid, receipt acknowledged, and a clearance to allow free circulation into the commerce of the country before the goods arrive. To make this happen, both documentation and payment submissions must be effected efficiently.
The documentation must be spelt out in the Incoterms® rule ancillary details as is shown in the example above. If this documentation is provided electronically within 24 hours of sailing, then a submission of the item’s details can be made as it leaves the sending country, or such other period as specified by the receiving country. This is while the goods are still well away from the country of final destination and allows some time for payments to be effected. Even if electronic submission is not allowed, it allows for documents to be couriered to the receiving country, and then prepared for manual submission.
The submissions to the customs authority will result in a statement of duties to be paid before the goods can be released for commerce in the destination country. The goods will remain within customs restriction until the duties are paid. In many countries the goods are held in customs-controlled yards or warehouses, and these often come with a charge. There is a financial incentive to be able to pay the duties quickly and in the most efficient way possible, be it electronically or manually, in order to minimize this time. Do not assume the banking system processes an electronic payment quicker than a manual one. It is very valuable to look at the process the banking system operates, determine the actual times, and see where and how to do these payments to minimize the delays. Financial systems are primarily focused on the approval and control of the funds moved, but the time from duties advice to payment received cycle is important with duty payments. If you move $10 million into a country per year, your cost of one day’s delay is about US$4,000 (at a 15 percent cost of capital), excluding the value of the goods being available earlier. Personal experience had the actual payment, receipt and acknowledgement of the payment in a Middle Eastern country at about 12 days. While the financial team thought they had paid in about eight days, we found the bank transfer of the electronic payment did not work for two days of the week, nor did the bank clear the payment for at least two days, so the whole process took an average of 12 days. We organized expedited payments within three days and saved significant time and money. All these funds and information flows can lead to delays, and you must measure the time for the major stages as Key Performance Indexes, whether this is an internal function or done by a customs broker.
All of this assumes the information flow does not encounter an issue with the customs authority. A query or misunderstanding can stall your movement for days to weeks. An inspection will cost you about a week and will result in a warehouse charge. None of these are anything but a cost and a major nuisance, so efforts to remove or reduce these are valuable.
The solution is correct documentation always, with speedy funds movement to pay duties and submission for entry as fast as is allowed. Your processes may have to be altered, but these are what you need to deliver goods in the shortest possible time.
As indicated, we will start to review the documentation in the next article.
Missed Jon Vogt’s Previous Articles? Find Them Here:
Why Everyone Needs a Better Understanding of Incoterms (January 11, 2022)
For Incoterms, Devil is in the Details (February 8, 2022)
Why Use Ex Works Incoterm Rule? (March 3, 2022)
When FCA Can Be a Four-letter Word (March 31, 2022)
Exploring the 'C' Rules for Cost and Carriage (June 10, 2022)
CPT, CIP Add to Complexity of Incoterm Rules (July 7, 2022)
Trade Game Often Needs a Good ‘D’ (August 4, 2022)
About the Author
John Vogt has his own consulting company and, at the end of his 42 years in industry around the world, was the Vice President of Global Logistics for Halliburton. Thereafter he spent five years as a Professor of Record for the University of Houston-Downtown MBA for International and Supply Chain courses. He has experience as a Board Director and has traveled the world to improve trade.
In his career, he has driven the correct use of Incoterms as part of the trade improvements he has implemented to drive efficiency and effectiveness. In his role as a professor of record, he taught multiple courses on the use of Incoterms and trade-related agreements. He has published with colleague Dr. Jonathan Davis (Associate Professor, Supply Chain Management Chair GMSC Department, Marilyn Davies College of Business, University of Houston-Downtown), three formal research papers on Incoterms with two more in consideration, making him the most published Incoterms researcher. He has also published numerous articles, presented papers at multiple international conferences around the world on logistics, trade and compliance including Incoterms. He has served as track chair for multiple conferences as well.
Vogt has a Ph.D. (Logistics), an MBA, and a B.Sc. (Engineering), holds the title of European Engineer (Eur. Ing), is a Chartered Engineer (UK) and has been elected as a Fellow of the Institute of Engineering and Technology (UK). You can reach him at [email protected].